Advanced ceramics such as Silicon Carbide (SiC) and Boron Carbide (B4C) are essential materials in modern technology, each possessing unique properties and applications that distinguish them from conventional materials. These ceramics are known for their exceptional hardness and durability, making them ideal for a variety of industrial uses. Silicon Carbide and Boron Carbide are used in applications ranging from abrasive materials to armor plating and advanced electronics, highlighting their versatility and critical role in technological advancements.
Silicon Carbide is a compound of silicon and carbon, known for its high thermal conductivity and electrical resistivity, making it popular in semiconductor electronics and high-temperature applications. Boron Carbide, on the other hand, is one of the hardest materials available, only surpassed by cubic boron nitride and diamond. It is highly valued in applications requiring high hardness combined with light weight, such as ballistic armor and abrasive industries.
Both materials exhibit remarkable properties such as high melting points, extreme hardness, and chemical inertness, but they also differ significantly in aspects like thermal conductivity and resistance to oxidation. These differences make each suitable for specific applications, where performance under stress and environmental conditions is critical.
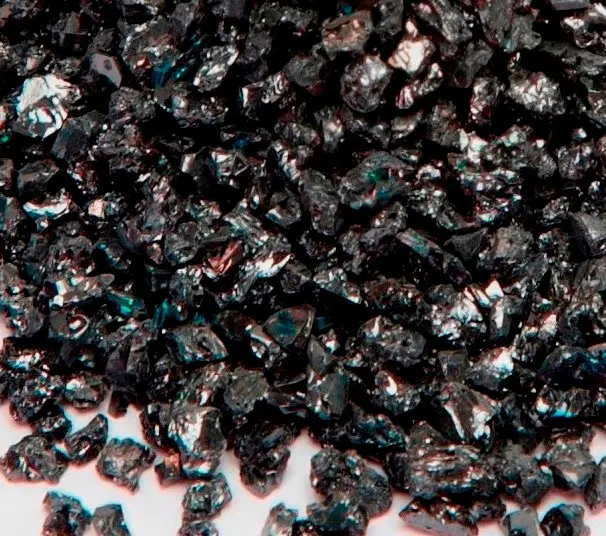
Properties Overview
Silicon Carbide Properties
Physical Properties
Silicon Carbide (SiC), a compound of silicon and carbon, is noted for its exceptional hardness that rivals diamonds. It possesses a hexagonal crystalline structure which contributes to its high hardness and strength. SiC also exhibits remarkable thermal shock resistance, meaning it can withstand sudden changes in temperature without fracturing. This material maintains its strength even at high temperatures, typically up to 1600°C, making it ideal for high-temperature applications.
Chemical Stability
One of the defining traits of Silicon Carbide is its chemical inertness. It does not react with acids or alkalis at room temperature and maintains its structure and functionality even under harsh chemical environments. This resistance to chemical attack makes SiC a preferred material in applications such as mechanical seals and chemical plant machinery.
Thermal Conductivity
Silicon Carbide is known for its excellent thermal conductivity. With values typically around 120 W/mK, it is used extensively in applications that require good heat dissipation such as in power electronics and high-performance brake systems. The ability of SiC to dissipate heat quickly also enhances its stability and longevity in electronic applications.
Boron Carbide Properties
Hardness and Density
Boron Carbide (B4C) stands out primarily for its incredible hardness, which is only surpassed by cubic boron nitride and diamond. It has a Mohs hardness of about 9.5, making it one of the hardest materials known. Despite its hardness, it has a lower density compared to other ceramics, at about 2.52 g/cm³, which contributes to its popularity in weight-sensitive applications like ballistic armor.
Chemical Resistance
B4C exhibits exceptional chemical stability and does not react with acids or bases, which makes it suitable for use in environments where corrosive agents are present. Its resilience to chemical erosion plays a vital role in extending the life and performance of equipment used in harsh environments.
Thermal Properties
Boron Carbide also exhibits good thermal properties. It withstands temperatures up to about 400°C before experiencing any form of thermal degradation. This attribute, combined with its low thermal expansion coefficient, makes it ideal for high-temperature applications that require a material to maintain its shape and size under thermal stress.
Production Methods
Silicon Carbide Synthesis
Acheson Process
The Acheson process is the primary method for producing Silicon Carbide. It involves heating a mixture of silica sand and carbon to high temperatures in an electric resistance furnace. The reaction produces SiC and carbon monoxide:
SiO2+3𝐶→SiC+2𝐶𝑂SiO2+3C→SiC+2CO
This method has been used since the late 19th century and continues to be the standard due to its cost-effectiveness and ability to produce high-purity SiC.
Other Manufacturing Techniques
Apart from the Acheson process, other techniques such as chemical vapor deposition (CVD) and sintering are also used to produce Silicon Carbide. These methods offer greater control over the properties of the final product, allowing for the creation of high-purity and finely-tuned SiC suitable for specific applications.
Boron Carbide Synthesis
Carbothermal Reduction
Carbothermal reduction is the most common method used to synthesize Boron Carbide. It involves the reduction of boron oxide with carbon at temperatures above 2000°C:
B2O3+3𝐶→B4C+3𝐶𝑂B2O3+3C→B4C+3CO
This process yields Boron Carbide powder, which can then be shaped and sintered into desired forms.
Other Synthesis Methods
Alternative methods such as the magnesiothermic reduction of boron oxide or the direct synthesis from elements at high temperatures are also employed to produce B4C. These methods allow for the production of Boron Carbide with different granularities and purity levels.
Applications
Silicon Carbide Uses
Industrial Applications
Silicon Carbide is utilized in various industrial applications due to its hardness and thermal properties. It is commonly found in abrasive and cutting tools, refractory linings, and as a component of high-strength ceramics. Its ability to withstand high temperatures and corrosive environments makes it an ideal choice for furnace components and kiln furniture.
Role in Electronics
SiC is increasingly used in power electronics. Its high thermal conductivity and electrical resistivity make it suitable for high-voltage, high-temperature applications such as diodes, transistors, and thyristors. SiC components are crucial in electric vehicles, solar power inverters, and high-power systems where efficiency and heat management are critical.
Boron Carbide Uses
Abrasives and Armors
Boron Carbide is extensively used as an abrasive material due to its high hardness. It is employed in polishing and lapping applications where materials harder than B4C are seldom found. In defense, Boron Carbide is a material of choice for body armor, providing protection against ballistic projectiles due to its lightweight and high hardness properties.
Nuclear Applications
The neutron absorption capability of Boron Carbide makes it invaluable in nuclear reactors as a control material. It absorbs neutrons without forming long-lived radionuclide, thus ensuring the safe and efficient control of nuclear reactions.
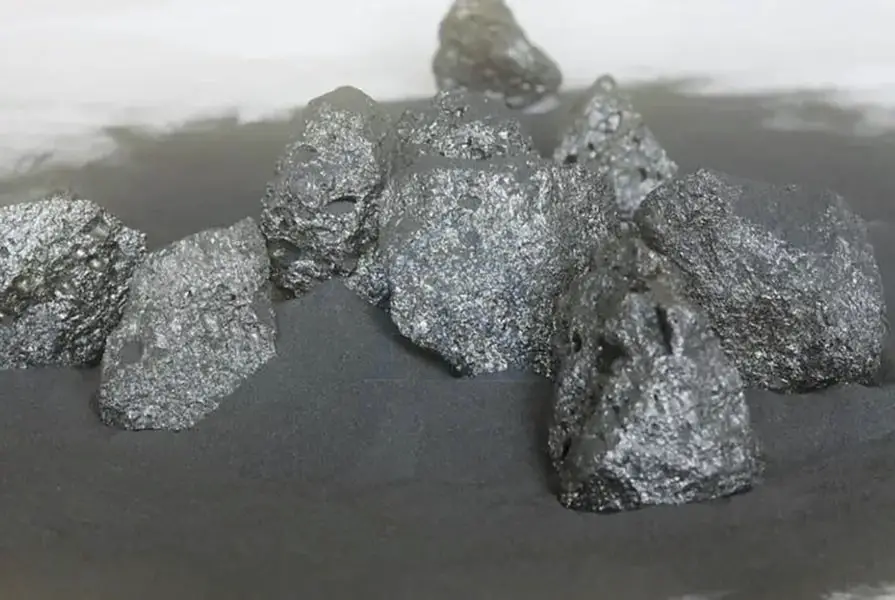
Performance Comparison
Hardness and Toughness
Comparative Analysis of Hardness
When comparing Silicon Carbide and Boron Carbide, both materials are renowned for their extreme hardness. Boron Carbide is the third hardest material, just after diamond and cubic boron nitride, making it slightly harder than Silicon Carbide. This hardness is crucial for applications requiring wear resistance and the ability to withstand high pressures.
Impact on Performance
The superior hardness of Boron Carbide provides enhanced wear resistance in abrasive environments, which is essential for protective gear and abrasive applications. Silicon Carbide, while slightly less hard, compensates with its thermal conductivity and toughness, making it ideal for high-stress, high-temperature applications. The toughness of SiC helps prevent brittle failure under mechanical stress, enhancing durability in industrial and electronic applications.
Thermal and Chemical Resistance
Thermal Stability in Extreme Conditions
Silicon Carbide excels in thermal stability. It can operate at temperatures up to 1600°C, significantly higher than Boron Carbide, which can handle up to 400°C. This makes SiC particularly valuable in applications such as automotive brakes and electronic components that must operate at high temperatures.
Resistance to Corrosive Environments
Both materials exhibit excellent resistance to corrosion. Silicon Carbide is inert to attacks by most acids and alkalis, maintaining integrity in harsh chemical environments like those found in semiconductor manufacturing and chemical processing plants. Similarly, Boron Carbide offers high resistance to chemical agents, ensuring longevity and reliability in abrasive and protective applications.
Cost and Availability
Market Trends
The market for Silicon Carbide and Boron Carbide has been expanding due to their increasing applications in technology and defense. The demand for SiC in semiconductor electronics and electric vehicles, and for B4C in armor and nuclear applications, is driving substantial growth in their markets.
Pricing Factors
The cost of Silicon Carbide and Boron Carbide is influenced by the purity of the material, the complexity of the synthesis process, and the scale of production. SiC tends to be less expensive due to the established and scaled-up production methods like the Acheson process. In contrast, Boron Carbide tends to be more costly due to its more complex production requirements and lower demand relative to SiC.
Availability in Global Markets
Silicon Carbide is widely available globally, with numerous suppliers and manufacturers in Europe, Asia, and North America. Boron Carbide, while also globally available, has fewer producers and is often sourced for specific applications, leading to slightly limited availability compared to SiC.
Future Prospects
Innovations in Material Science
Recent advancements in material science continue to enhance the properties and applications of both Silicon Carbide and Boron Carbide. Innovations include the development of composite materials that incorporate SiC and B4C to create solutions tailored for specific industrial needs, offering better performance and durability.
Recent Developments
Recent developments in the production processes of SiC and B4C aim to improve the efficiency and environmental impact of their synthesis. These include lower temperature synthesis processes that reduce energy consumption and advanced purification methods that enhance the quality and performance of the final product.
Potential Future Applications
The future applications for Silicon Carbide and Boron Carbide are promising and diverse. SiC is poised to play a crucial role in next-generation power electronics for renewable energy systems and smarter power grids. B4C is being explored for its potential in more effective neutron absorption materials in nuclear reactors and in advanced armor systems that offer higher protection with less material weight.
Environmental Impact
Sustainability Factors
The sustainability of producing Silicon Carbide and Boron Carbide focuses on minimizing environmental impacts. This involves optimizing manufacturing processes to consume less energy and produce fewer emissions, as well as developing recycling protocols for post-use materials.
Recycling and Reuse
Efforts to recycle and reuse Silicon Carbide and Boron Carbide are integral to reducing the environmental footprint of these materials. Recycling methods are being developed to reclaim SiC and B4C from waste products and used equipment, allowing for the recovery of valuable materials and reducing the need for raw material extraction.
Environmental Considerations in Production
Production of SiC and B4C involves high-temperature processes that can be energy-intensive. Recent technological advancements aim to reduce these environmental impacts by enhancing the efficiency of production methods and incorporating renewable energy sources into the manufacturing process. These measures not only improve the environmental profile of these materials but also align with global sustainability goals.
Frequently Asked Questions
What is Silicon Carbide?
Silicon Carbide is a synthetic mineral known for its extreme hardness and high thermal conductivity. It is commonly used in high-stress applications like semiconductor electronics, car brakes, and various high-temperature applications.
How is Boron Carbide manufactured?
Boron Carbide is produced through a process known as carbothermal reduction, where boron oxide is reacted with carbon at high temperatures. This method yields a material that is exceptionally hard and lightweight, making it ideal for protective gear and abrasive materials.
What are the main uses of Boron Carbide?
Boron Carbide’s primary applications include being used as an abrasive in grinding and lapping applications and as body armor due to its high hardness and light weight. It is also utilized in neutron radiation shields thanks to its high neutron absorption capabilities.
How does Silicon Carbide differ from Boron Carbide?
While both materials are extremely hard and chemically stable, Silicon Carbide has a higher thermal conductivity, making it better suited for electronic applications where heat dissipation is crucial. Boron Carbide, however, has a higher neutron absorption, making it indispensable in nuclear applications.
Conclusion
Silicon Carbide and Boron Carbide represent pinnacle achievements in materials science, each serving critical roles across a spectrum of industries. Their unique characteristics of hardness, thermal stability, and chemical resistance make them indispensable in both everyday and specialized applications. The ongoing development and research into these materials promise even greater advancements and potential uses in the future.
As technology continues to evolve, the applications and importance of Silicon Carbide and Boron Carbide are likely to expand, further underscoring their significance in modern engineering and technology. Their continued study and refinement will undoubtedly unlock new possibilities, enhancing both their efficiency and scope of application.