Metalworking is an age-old craft that has evolved significantly with technological advancements. Among the myriad of processes that metalworkers employ, sintering and annealing stand out due to their critical roles in enhancing the properties of metals. These techniques are fundamental in the production and treatment of various metal products, influencing their durability, strength, and usability.
Sintering and annealing are thermal processes used to alter the physical and sometimes chemical properties of materials. Sintering involves heating powder metal to just below its melting point to fuse particles together, while annealing heats metal above its recrystallization temperature and then cools it slowly to remove internal stresses and soften the material. Both processes are pivotal in preparing metals for further use or improving their mechanical properties.
The choice between sintering and annealing depends on the desired characteristics of the metal. Sintering is essential for creating complex shapes and achieving high strength in metals without melting them completely. Annealing, on the other hand, is crucial for improving ductility and reducing hardness, making metals easier to work with. Understanding the distinct purposes and outcomes of these processes helps in selecting the appropriate treatment for different metalworking projects.
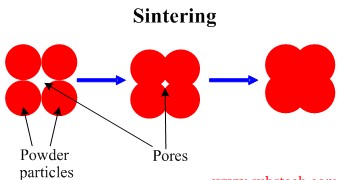
Basics of Sintering
Definition and Process
Sintering is a heat treatment process used to create a solid mass from powdered materials without melting them to the point of liquefaction. This technique involves applying heat below the material’s melting point but at a level high enough to allow atoms in the powder particles to fuse by diffusion. The process can be broken down into three main stages:
- Initial Heating: The powdered material is heated in a controlled environment, leading to neck formation at points where particles touch.
- Intermediate Stage: As the temperature increases, diffusion accelerates, causing particles to bond more significantly and the mass to densify.
- Final Stage: The material is cooled down slowly to solidify the structure, creating a dense, unified mass.
Types of Sintering
Sintering can be categorized into several types based on the method and conditions applied. The most common types include:
Pressureless Sintering
This is the standard method where the material is heated in a furnace without external pressure, relying solely on the heat to facilitate particle fusion.
Hot Pressing
Involves applying heat and mechanical pressure simultaneously to compact the powder into a dense form more quickly than pressureless sintering.
Spark Plasma Sintering (SPS)
A rapid sintering process that uses a pulsed electric current to activate the powder particles, leading to faster diffusion and densification.
Applications
Sintering plays a crucial role in manufacturing components across various industries, thanks to its ability to produce complex shapes and high-strength parts. Common applications include:
- Automotive parts such as gears and filters
- Electrical components like capacitors and inductors
- Medical implants and dental restorations
- Aerospace components, offering lightweight yet strong materials
Basics of Annealing
Definition and Process
Annealing is a heat treatment process aimed at reducing hardness, improving ductility, and relieving internal stresses within metals. The process involves three key steps:
- Heating: The metal is heated to a specific temperature, typically above its recrystallization temperature, allowing new grains without pre-existing stresses to form.
- Soaking: The metal is held at the target temperature for a period, ensuring uniform heat penetration.
- Cooling: It is cooled down slowly, often in the furnace, to room temperature, which results in a softer and more workable metal.
Types of Annealing
Annealing can be divided into various categories based on the cooling method and the atmosphere in the furnace. Key types include:
Full Annealing
The metal is heated above its recrystallization temperature and then cooled slowly in the furnace, maximizing ductility.
Process Annealing
Also known as subcritical annealing, this involves heating the metal below its recrystallization temperature and cooling it at a controlled rate to reduce hardness without significantly altering the structure.
Spheroidizing
A specialized form of annealing aimed at producing a spherical or globular form of carbide within the steel to enhance its machinability.
Applications
Annealing is widely used in various industries to improve metal workability and prepare it for subsequent manufacturing processes. Key applications include:
- Improving machinability of metals like steel and aluminum
- Preparing for further heat treatment processes by softening and making materials more ductile
- Enhancing electrical conductivity in materials like copper and silver
- Stress relieving in welded or cast products to improve their durability
Key Differences
Process Temperatures
The temperature at which sintering and annealing occur is a fundamental difference. Sintering temperatures are below the melting point of the base metal but high enough to facilitate particle bonding. Annealing, however, involves heating the metal above its recrystallization temperature and then cooling it slowly to alter its microstructure and mechanical properties.
Material Structure Changes
Sintering and annealing affect the material structure in distinct ways. Sintering densifies the material by bonding powder particles at a high temperature, enhancing strength without melting. Annealing alters the crystal structure of the metal, reducing internal stresses and improving ductility and machinability.
Mechanical Properties Affected
The mechanical properties of materials are significantly impacted by these processes. Sintering increases the material’s strength and hardness by compacting the powder into a dense mass. Annealing, in contrast, softens the metal, enhancing its ductility and reducing brittleness.
Common Materials Processed
Both processes are applicable to a wide range of materials, but their suitability varies. Sintering is commonly used with metals, ceramics, and polymers that can be powdered and fused at high temperatures. Annealing is typically applied to metals like steel, copper, aluminum, and brass to improve their workability and reduce hardness.
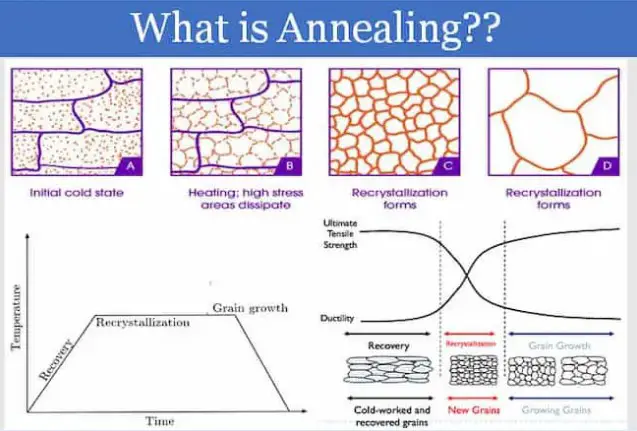
Process Comparison
Temperature Range
The temperature range at which sintering and annealing are performed is a key differentiator between these two processes, impacting the final properties of the treated materials.
Sintering Temperature Specifics
Sintering typically occurs at temperatures between 70% and 90% of the material’s melting point. This range is crucial for facilitating particle bonding without complete melting. For metals, this can vary widely:
- Steel and iron powders: 1120°C to 1300°C
- Aluminum alloys: 550°C to 650°C
- Ceramic materials: can exceed 1800°C
These temperatures ensure the powdered material densifies through diffusion, significantly altering its physical properties without changing its phase.
Annealing Temperature Specifics
Annealing involves heating a material above its recrystallization temperature but well below its melting point, followed by controlled cooling. Specific temperatures depend on the material:
- Steel: 700°C to 1300°C, depending on the alloy and desired results
- Copper: 350°C to 650°C
- Aluminum: 280°C to 350°C
This process aims to relieve internal stresses, improve ductility, and reduce hardness by allowing the formation of new, stress-free grains.
Material Structure
Microstructure Changes in Sintering
During sintering, the microstructure of the material undergoes significant transformation. The process starts with powder particles that have distinct boundaries. As the temperature increases:
- Particle Bonding: Begins at contact points, growing necks between particles.
- Pore Reduction: Pores between particles shrink, increasing density.
- Grain Growth: Grains start to grow within individual particles, merging across boundaries.
This evolution results in a more uniform and densified material with enhanced physical properties.
Microstructure Changes in Annealing
Annealing changes the microstructure by:
- Stress Relief: Reducing dislocations and internal stresses within the grains.
- Grain Recrystallization: Formation of new grains without the pre-existing stress.
- Grain Growth: Larger grains grow at the expense of smaller ones, leading to a more ductile and less hard material.
These changes improve the workability and reduce the hardness of the metal, making it suitable for further processing.
Outcome and Applications
Impact on Mechanical Properties
Sintering enhances the material’s strength, wear resistance, and overall durability by compacting the powder into a dense, coherent mass. It is particularly beneficial for creating parts with complex geometries that are difficult to achieve through traditional metalworking techniques.
Annealing increases the ductility and reduces the hardness of metals, making them easier to work with. This process is essential for materials that will undergo further deformation or shaping, as it helps to prevent cracking and failure.
Preferred Applications for Each
Sintering is often chosen for manufacturing components that require high precision and strength, such as gears, bearings, and filters. It is also used in the production of complex shapes in ceramics and metals that cannot be easily achieved through other methods.
Annealing is widely used in the metal industry to prepare materials for further processing, including machining, shaping, and welding. It is also crucial in the electronics industry, where it enhances the electrical conductivity of metals like copper and aluminum.
Advantages and Limitations
Sintering
Advantages
- Complex Shapes: Allows for the creation of complex and precise shapes.
- Material Efficiency: Minimizes waste, as materials can be fully used.
- Enhanced Properties: Provides parts with high density and strength.
Limitations
- Cost: High initial setup and equipment costs.
- Material Limitations: Not all materials can be effectively sintered.
- Size Limitations: Typically used for smaller components due to equipment size constraints.
Annealing
Advantages
- Improved Ductility: Makes materials softer and more pliable.
- Stress Reduction: Reduces internal stresses, preventing material failure.
- Versatility: Can be applied to a wide range of metals and alloys.
Limitations
- Time-Consuming: The slow cooling process can be time-intensive.
- Energy Consumption: Requires significant energy for heating.
- Control: Requires precise control over temperature and cooling rates.
Selecting the Right Process
Factors to Consider
When choosing between sintering and annealing, several factors must be considered:
- End-Use Requirements: Desired mechanical properties and part complexity.
- Material: Not all materials are suitable for both processes.
- Cost: Budget constraints and cost-effectiveness of each method.
Material Compatibility
Understanding the material’s response to heat is crucial. While sintering is ideal for powders and materials that benefit from increased density and strength, annealing is suited for metals that need enhanced ductility and reduced hardness.
Desired Mechanical Properties
The choice between sintering and annealing also hinges on the final mechanical properties required:
- For higher strength and wear resistance: Sintering might be the preferred choice.
- For improved ductility and workability: Annealing is often more appropriate.
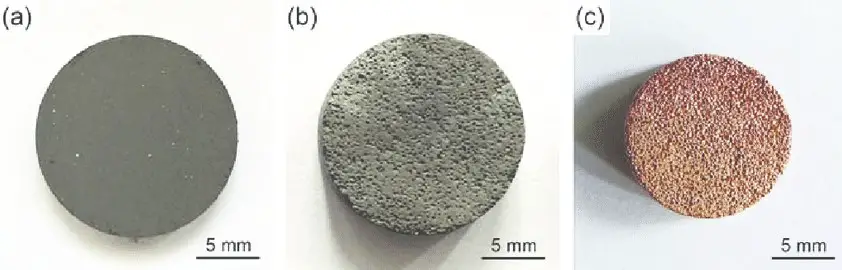
Frequently Asked Questions
What is the main purpose of sintering?
Sintering aims to create a solid mass from powder by applying heat without melting the material completely. This process is vital for producing complex shapes and achieving a high level of strength in metals, ceramics, and other powdered materials.
How does annealing improve metal properties?
Annealing improves metal properties by heating the material above its recrystallization temperature and then allowing it to cool slowly. This process reduces internal stresses, increases ductility, and decreases hardness, making the metal easier to shape and work with.
Can sintering and annealing be used on all metals?
Not all metals are suitable for sintering and annealing. These processes are material-specific, with certain metals and alloys responding better to either sintering or annealing based on their melting points, thermal conductivity, and other physical properties.
What are the key differences between sintering and annealing?
The key differences between sintering and annealing lie in their temperature ranges, the changes they induce in material structure, and the mechanical properties they affect. Sintering involves heating below the melting point to bond particles, while annealing involves heating above the recrystallization temperature followed by controlled cooling to alter the metal’s internal structure.
Conclusion
Sintering and annealing are pivotal processes in the field of metalworking, each serving distinct purposes that significantly impact the properties and usability of metals. Through sintering, manufacturers can produce complex and strong metal components without fully melting the material, while annealing allows for the enhancement of ductility and the reduction of hardness, making metals more workable.
Understanding the nuances of these processes is crucial for selecting the right treatment for specific applications. This knowledge not only ensures the durability and functionality of metal products but also opens avenues for innovation in metalworking techniques, showcasing the intricate balance between science and craftsmanship in the industry.