Heat treatment processes are essential in material engineering to enhance the properties of metals, making them suitable for various industrial applications. Among these, carburizing and carbonitriding stand out as two critical methods used to improve the surface hardness and wear resistance of steel parts. Both processes involve the introduction of carbon into the metal, but they differ in their approach and the resulting material characteristics.
Carburizing involves enriching the surface layer of steel with carbon to increase hardness and resistance to wear, whereas carbonitriding additionally incorporates nitrogen, offering distinct advantages under certain conditions. The choice between these two processes often depends on the specific requirements of the application, such as the desired hardness, environmental resistance, and the type of steel used.
Understanding the differences between carburizing and carbonitriding is crucial for selecting the appropriate heat treatment process. Each method not only serves to enhance the durability and functionality of metal components but also influences manufacturing costs and production efficiency. As industries strive for higher performance and longer-lasting materials, knowing these processes helps in making informed decisions tailored to operational needs.
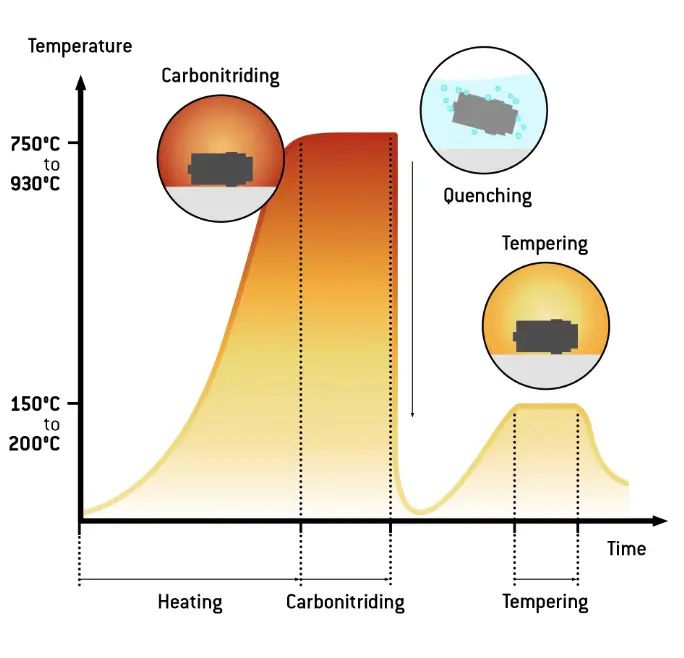
Carburizing Explained
Definition and Process
Carburizing, also known as case hardening, is a heat treatment technique used to increase the surface hardness of low carbon steel by diffusing carbon into the outer layer of the metal. This process occurs in a high-temperature environment where the steel is exposed to a carbonaceous atmosphere. The result is a significantly hardened surface over a more ductile core, which enhances the steel’s overall durability and wear resistance.
Types of Carburizing
There are three primary types of carburizing used today:
- Gas Carburizing: The most common form, involving a carbon-rich gas environment, typically using methane or propane.
- Liquid Carburizing: Steel parts are immersed in a bath of molten carbon-containing material, such as cyanide.
- Vacuum Carburizing: A modern method that provides precise control over the carburizing atmosphere and depth, using a vacuum chamber.
Materials Suitable for Carburizing
The best candidates for carburizing are typically low-carbon steels and low-alloy steels. These materials include:
- AISI 1010
- AISI 1020
- AISI 8620
- Other low alloy steels like 41xx series
Industrial Applications
Carburizing is widely used in various industries due to its ability to significantly enhance the life and performance of steel components. Key applications include:
- Gear manufacturing
- Automotive axles and drive trains
- High-stress machinery components
Carburizing Benefits
Enhanced Surface Hardness
Through carburizing, the steel’s surface hardness is significantly increased, making it resistant to surface wear and extending the component’s operational life.
Improved Wear Resistance
The harder surface significantly reduces the wear rate of steel components, which is crucial in high-friction environments such as automotive and heavy machinery.
Case Depth Implications
The depth of the hardened layer, or case depth, can be controlled based on the carburizing duration and temperature, allowing for tailored properties based on specific needs.
Carburizing Limitations
Potential for Distortion
During carburizing, the steel may distort due to the high temperatures and carbon absorption, which may require further processing to achieve dimensional accuracy.
Surface Carbon Inconsistencies
Uneven carbon distribution can lead to inconsistencies in hardness and brittleness across the treated surface.
Environmental Concerns
Traditional carburizing methods, especially those using cyanide baths, pose significant environmental and safety risks.
Carbonitriding Overview
Definition and Process Contrast
Carbonitriding, similar to carburizing, involves the addition of carbon to the steel’s surface. However, it distinguishes itself by also incorporating nitrogen into the process. This typically happens at lower temperatures compared to carburizing and involves using gaseous ammonia as a nitrogen source, which penetrates along with carbon into the steel.
Carbonitriding vs. Carburizing
While both processes aim to enhance surface hardness, carbonitriding allows for:
- Harder surfaces due to the combined effect of carbon and nitrogen.
- Better adhesion and stability under high temperatures.
Suitable Materials
Carbonitriding is particularly effective on:
- Low carbon steels
- Alloy steels not suitable for traditional carburizing
- Parts that require a thin but hard surface
Industrial Uses
This process finds its applications in industries where high surface hardness and low core deformability are required, such as:
- Automotive gears and bearings
- Firearms manufacturing
- Aerospace fasteners and gear components
Carbonitriding Benefits
Improved Surface Hardness and Toughness
The dual incorporation of carbon and nitrogen not only increases surface hardness but also improves the toughness, making the steel less prone to cracking under stress.
Less Distortion Compared to Carburizing
As it operates at lower temperatures, carbonitriding causes less distortion, reducing the need for post-treatment machining.
Enhanced Fatigue Strength
The treated components exhibit superior fatigue strength, crucial for parts subjected to cyclic loading.
Carbonitriding Challenges
Process Complexity
The addition of nitrogen and the need for precise control over gas composition make carbonitriding a more complex process than standard carburizing.
Higher Cost Implications
The complexity and control required in carbonitriding typically lead to higher operational costs.
Temperature Sensitivity
The lower temperatures used in carbonitriding, while reducing distortion risks, require precise management to achieve the desired hardness and depth.
Comparative Analysis
Process Temperatures
Carburizing typically occurs at temperatures ranging from 900°C to 950°C, which is necessary to enable carbon atoms to penetrate the steel surface effectively. In contrast, carbonitriding is performed at slightly lower temperatures, generally between 820°C and 880°C. This difference affects not only the process efficiency but also the properties of the treated metal, including grain size and microstructure stability.
Depth of Hardening
The depth of hardening, or case depth, is a critical factor in determining the performance of the heat-treated part. Carburizing can produce a significantly deeper hardened layer, often up to 1.5 mm, which is ideal for components that must withstand high levels of stress and wear. Carbonitriding, while typically achieving shallower depths of around 0.25 mm to 0.75 mm, allows for the creation of a hard surface on parts that also require a high degree of core ductility.
Cost-effectiveness
When considering cost-effectiveness, carburizing tends to be less expensive due to simpler gas atmospheres and longer-established practices. However, carbonitriding can be more cost-effective over the long term for parts that require less post-process machining due to its lower distortion rates.
Environmental Impact
The environmental impact of both processes is significant but differs in nature. Carburizing often uses potentially harmful chemicals in its gas atmospheres, such as methane and propane. Carbonitriding, which involves ammonia, presents risks associated with nitrogen emissions. Modern advancements strive to mitigate these impacts through recycling and cleaner technologies.
Decision Factors
Material Selection
The choice of material significantly influences whether carburizing or carbonitriding is more appropriate:
- Low carbon steels: Both processes are suitable, but the specific alloying elements may sway the decision.
- Alloy steels: Typically prefer carbonitriding due to its ability to harden a wider range of alloys effectively.
Desired Properties
The required properties of the final product, such as wear resistance, toughness, and thermal stability, play a crucial role in deciding between carburizing and carbonitriding.
Application Requirements
The specific requirements of the application, including operating environment, stress levels, and expected lifespan, dictate the heat treatment process to ensure optimal performance and durability.
Case Studies
Automotive Industry Applications
In the automotive sector, carburizing is extensively used for gear parts, axles, and drive shafts, where surface durability and fatigue resistance are paramount. Carbonitriding, meanwhile, is preferred for components like bearings and fasteners that benefit from its enhanced surface hardness and reduced distortion.
Aerospace Component Enhancements
Aerospace applications often involve extreme conditions, requiring materials that can withstand high pressures and temperatures. Carbonitriding is employed for critical fasteners and gears in aircraft engines, where its superior surface hardness and reduced risk of fatigue are crucial.
Tool and Die Sector Examples
In the tool and die industry, carburizing helps extend the life of tools by improving their wear resistance. Carbonitriding is used for dies that require a hard surface to withstand repeated impacts without compromising the tool’s toughness.
Future Trends
Advances in Heat Treatment Technologies
The ongoing development in heat treatment technologies focuses on enhancing efficiency and reducing environmental impact. Innovations such as pulse plasma carburizing and low-pressure carbonitriding are gaining traction, offering finer control over case depth and uniformity.
Environmental Regulations Impact
As environmental regulations become stricter, the heat treatment industry is adapting by implementing cleaner and more sustainable practices. This includes using less toxic chemical sources and developing methods that minimize energy consumption and emissions.
Industry Adoption and Adaptations
Industries are increasingly adopting these advanced heat treatment processes to not only comply with environmental guidelines but also to improve product performance and reduce lifecycle costs. This shift is evident in sectors such as automotive and aerospace, where material properties directly influence the safety and efficacy of the end product.
FAQs
What is carburizing?
Carburizing is a heat treatment process that involves heating steel components in the presence of a carbon-rich environment. This method is primarily used to increase the surface hardness and wear resistance of the steel by diffusing carbon into the outer layers of the metal, creating a hardened case over a tougher core.
How does carbonitriding differ from carburizing?
Carbonitriding is similar to carburizing but involves the addition of nitrogen along with carbon in the heat treatment process. This modification generally occurs at lower temperatures and results in a thinner, harder case compared to carburizing, making it ideal for parts that require both surface hardness and core toughness.
What are the advantages of carbonitriding over carburizing?
Carbonitriding often results in a harder surface and better wear resistance with less risk of distortion during the heat treating process. It is particularly effective on lower-grade steels that cannot undergo traditional carburizing due to their alloy content, making it a versatile choice for a wider range of applications.
When should I choose carburizing over carbonitriding?
Choose carburizing when you need deeper case depths for components that will undergo extreme pressures or wear conditions. It is particularly suitable for high-quality alloy steels and is often preferred for its ability to produce a thick, durable layer that enhances the lifespan and performance of heavy-duty mechanical parts.
Conclusion
The decision between carburizing and carbonitriding hinges on the specific requirements of the application, the properties desired in the finished product, and the type of steel used. Both processes enhance the mechanical properties of steel components, but the choice must align with operational demands and environmental conditions to maximize efficiency and cost-effectiveness.
In the evolving field of material engineering, staying informed about the capabilities and differences of these heat treatment processes is essential. As technology advances, the methods to optimize the performance of steel parts continue to improve, making the knowledge of carburizing and carbonitriding invaluable for engineers and manufacturers aiming to achieve the highest standards in product durability and performance.