Sodium silicate and sodium metasilicate, though sounding similar, are distinct compounds with unique properties and applications. Often used in industries ranging from manufacturing to consumer goods, these chemicals play integral roles but are frequently misunderstood or confused with one another. Both are derivatives of silica and sodium oxide, yet their chemical structure and implications vary significantly.
Sodium silicate, commonly referred to as water glass, is a versatile compound used in a variety of applications, including as an adhesive, in detergents, and in water treatment. Sodium metasilicate, on the other hand, serves as a key ingredient in industrial cleaning agents and concrete treatments, offering a slightly different set of properties tailored for more specific uses. These differences are crucial for industries relying on their unique characteristics for efficient and effective results.
Despite their industrial importance, the environmental and health implications of these compounds are significant. Both chemicals require careful handling due to their corrosive nature and potential environmental impact. Understanding their distinct properties helps in utilizing them safely and sustainably in their respective applications.
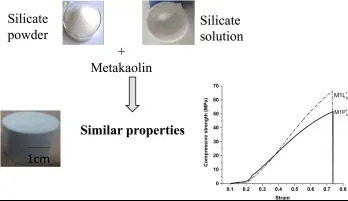
Chemical Properties
Sodium Silicate
Basic Composition
Sodium silicate, commonly known as liquid glass or water glass, is a chemical compound comprising sodium oxide (Na2O) and silicon dioxide (SiO2) dissolved in water. The compound typically appears in a range of ratios between sodium oxide and silicon dioxide, influencing its properties and applications. These ratios are crucial as they determine the viscosity, binding capabilities, and solubility of the sodium silicate solutions.
Physical Form
In its commercial form, sodium silicate is available either as a solid, lumpy, granular, or powdered substance or more commonly as a thick, viscous aqueous solution. This diversity in physical form allows it to be versatile in various applications, adjusting the concentration and dilution according to specific needs.
Sodium Metasilicate
Basic Composition
Sodium metasilicate is a chemical entity with the formula Na2SiO3. It differs from sodium silicate primarily in its silica to sodium ratio, which is fixed and thus offers less variability in its interaction properties. This consistency is critical for applications requiring precise chemical reactions and formulations.
Physical Form
Sodium metasilicate is typically found as a white crystalline powder or as pentahydrate granules when water is added. Its high solubility in water and rapid dissolution rate make it ideal for formulations where quick and complete dissolving of the chemical is necessary.
Production Processes
Sodium Silicate
Overview of Production Methods
Sodium silicate is produced using a high-temperature reaction between silica (sand) and sodium carbonate (soda ash). This process occurs in a direct fired furnace where the raw materials are heated to temperatures up to 1400°C, forming a molten glass which is then dissolved in water.
Key Raw Materials
The primary materials for sodium silicate production are:
- Silica sand, which provides the silicon dioxide.
- Sodium carbonate, commonly known as soda ash, which supplies the sodium oxide.
These ingredients are abundant and relatively inexpensive, contributing to the widespread use of sodium silicate in various industries.
Sodium Metasilicate
Overview of Production Methods
The production of sodium metasilicate typically involves the fusion of silicon dioxide with sodium oxide at high temperatures. Unlike sodium silicate, the process ensures a precise stoichiometric ratio in a controlled environment to achieve the desired product consistency.
Key Raw Materials
Sodium metasilicate relies on similar raw materials as sodium silicate but with stricter control over the purity and proportions:
- High-purity quartz sand to ensure consistent silicon content.
- Refined sodium carbonate to maintain the accuracy of the sodium content.
Industrial Applications
Sodium Silicate Uses
In Detergents
Sodium silicate serves as a crucial ingredient in detergent formulations. It functions as a:
- Builder to enhance the cleaning efficiency.
- Buffer to maintain the necessary pH for optimum detergent performance.
- Corrosion inhibitor to protect washing machine parts.
In Cement and Construction
In the construction industry, sodium silicate is valued for its use as:
- Concrete sealer to reduce porosity and enhance durability.
- Cement binder to improve the strength of cement mixes.
Sodium Metasilicate Uses
In Cleaning Agents
Due to its powerful degreasing properties, sodium metasilicate is commonly found in:
- Industrial cleaners, particularly for degreasing and cleaning in automotive and aerospace industries.
- Dishwashing products, where it acts as a grease cutter and buffer.
In Textile Industries
In the textile sector, sodium metasilicate is used for:
- Textile processing to assist in the breakdown of natural fibers for bleaching and dyeing.
- Cleaning textile machinery, ensuring that equipment is free from contaminants and operational residues.
Environmental Impact
Sodium Silicate
Ecological Effects
Sodium silicate poses certain environmental challenges. Primarily, it can increase the pH of water bodies if discharged in significant quantities, which might lead to alkalinity that can be harmful to aquatic life. Its gelatinous precipitate can also clog waterways and affect the natural flow and filtering processes of ecosystems.
Disposal Considerations
Proper disposal of sodium silicate requires:
- Neutralization of its highly alkaline solutions before discharge.
- Compliance with local environmental regulations to prevent contamination.
- Collaboration with waste management services to ensure it does not mix with acids, which can lead to hazardous situations.
Sodium Metasilicate
Ecological Effects
Similar to sodium silicate, sodium metasilicate can disrupt aquatic environments by significantly raising pH levels. It requires careful monitoring to avoid environmental degradation, particularly in areas surrounding industrial discharge zones.
Disposal Considerations
Disposing of sodium metasilicate involves:
- Dilution to reduce the concentration of alkaline solutions.
- Regulatory adherence to ensure that disposal methods meet environmental safety standards.
- Controlled environments for disposal to prevent any reactions that could lead to hazardous byproducts.
Health and Safety
Handling Sodium Silicate
Safety Measures
To safely handle sodium silicate, individuals and industries should:
- Use protective gear, such as gloves and goggles.
- Ensure proper ventilation in areas where sodium silicate is processed or stored.
- Train employees on the risks and appropriate handling procedures.
Health Risks
Exposure to sodium silicate can result in:
- Skin irritation or burns from prolonged contact.
- Respiratory issues if inhaled, especially in powder form.
- Eye damage, potentially severe if contact occurs.
Handling Sodium Metasilicate
Safety Measures
Handling sodium metasilicate also demands caution, with necessary safety protocols including:
- Protective clothing to guard against chemical burns.
- Eye wash stations readily accessible in case of exposure.
- Strict handling guidelines to prevent accidental exposure.
Health Risks
The health risks associated with sodium metasilicate include:
- Chemical burns on skin or tissues.
- Potential toxicity if ingested, particularly in large amounts.
- Respiratory complications from inhalation of dust particles.
Economic Aspects
Market Dynamics
Global Demand for Sodium Silicate
The demand for sodium silicate is driven by its broad application in industries such as:
- Adhesives and sealants, where its binding properties are invaluable.
- Water treatment, where it acts as a flocculant to purify water.
Global Demand for Sodium Metasilicate
Sodium metasilicate enjoys robust demand in sectors like:
- Cleaning products, due to its effectiveness as a degreaser.
- Paper production, where it is used in de-inking recycled paper.
Cost Analysis
Production Costs
The production costs for these compounds depend largely on the availability and cost of raw materials, such as silica sand and soda ash, and the energy required for their high-temperature synthesis.
Market Pricing Trends
Market prices for sodium silicate and sodium metasilicate generally follow the trends in industrial demand and raw material costs, with regional variations reflecting local supply chain dynamics and regulatory impacts.
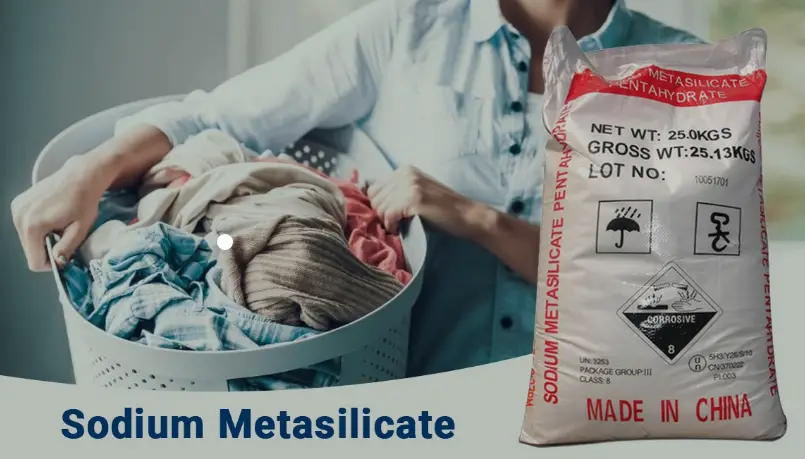
Advantages and Disadvantages
Benefits of Sodium Silicate
Cost-effectiveness
Sodium silicate is relatively inexpensive to produce, making it an economically viable option for many applications.
Versatility in Applications
Its uses range from everyday items like soaps and detergents to industrial applications such as welding and steel refining, highlighting its versatility.
Benefits of Sodium Metasilicate
Specific Use Advantages
Sodium metasilicate excels in applications requiring a consistent, strong alkali, such as in certain types of chemical cleaners and textile processing.
Efficiency in Certain Applications
It provides enhanced efficiency in settings that demand a rapid and robust alkaline reaction, like in metal cleaning and refining.
Drawbacks
Limitations of Sodium Silicate
Despite its benefits, sodium silicate is limited by its solubility and stability, which can affect its performance in fluctuating pH conditions.
Limitations of Sodium Metasilicate
Sodium metasilicate, while useful, must be handled with greater care due to its more caustic nature and higher reactivity, which can restrict its use in more sensitive environments.
Frequently Asked Questions
What is Sodium Silicate?
Sodium silicate, also known as liquid glass, is a compound made of silicon, oxygen, and sodium. It is predominantly used as an adhesive and sealant due to its capability to form a hard, protective layer when exposed to air.
What is Sodium Metasilicate?
Sodium metasilicate is a chemical derived from sodium oxide and silicon dioxide. It is highly effective as a cleaning agent and is commonly used in formulations for degreasers and detergents.
How do Sodium Silicate and Sodium Metasilicate differ?
The main difference lies in their chemical compositions and the ratio of silica to sodium oxide. Sodium silicate typically has a variable ratio which affects its viscosity and binding properties, whereas sodium metasilicate has a fixed ratio, making it more consistent for specific applications.
Are Sodium Silicate and Sodium Metasilicate environmentally safe?
Both compounds can pose environmental risks if not managed properly. They need to be treated and disposed of in accordance with safety regulations to mitigate any harmful effects on the environment.
Can Sodium Silicate and Sodium Metasilicate be used interchangeably?
While both compounds are used in industrial applications, they are not typically interchangeable due to their differing chemical properties and the resulting functional differences in end-use applications.
Conclusion
In conclusion, while sodium silicate and sodium metasilicate are closely related, their distinct differences define their applications and handling requirements. The proper understanding and utilization of each compound can lead to more effective and safe industrial processes. Future advancements in industrial chemistry may continue to expand the uses of these versatile compounds, but it remains essential to consider their environmental and health impacts to ensure sustainable practices.