Plastics are integral to modern life, found in everything from packaging to parts in high-tech devices. Two of the most common types are Polypropylene (PP) and Polyethylene Terephthalate (PET). These materials, though often used interchangeably by the layperson, possess distinct characteristics and uses that set them apart in the vast world of polymers.
PP and PET are both polymers widely utilized across various industries, but they differ significantly in their chemical composition and properties. PP is known for its flexibility, resistance to chemicals, and high melting point, making it ideal for containers that must endure heat. PET, on the other hand, is valued for its strength, clarity, and ability to be easily recycled, commonly found in beverage bottles and packaging.
In everyday items around us, from the plastic bottle that holds your water to the container that keeps your lunch fresh, PP and PET play pivotal roles. Their selection and use are dictated by their properties, which in turn are influenced by their unique molecular structures and the specific needs they meet in applications ranging from textiles to automotive components.
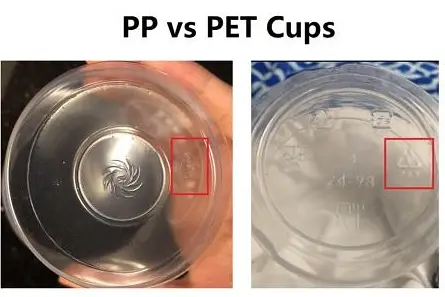
Basic Properties
PP Characteristics
Chemical Structure
Polypropylene (PP) is a thermoplastic polymer, which means it becomes pliable or moldable at a certain elevated temperature and solidifies upon cooling. Chemically, it is composed of propylene monomers, represented as C3H6. This structure grants PP its characteristic properties such as high chemical resistance and a high melting point, which are key to its utility in a wide range of applications.
Physical Properties
PP is distinguished by several notable physical properties:
- Durability and Toughness: Despite being lightweight, PP is exceptionally resistant to stress and cracking, which is why it is used in products that require ruggedness.
- Heat Resistance: With a melting point of around 160°C, PP can withstand higher temperatures compared to many other plastics, making it suitable for microwave containers and dishwasher-safe products.
- Flexibility: Depending on the manufacturing process, PP can be made flexible enough for use in applications such as flexible packaging and tubing.
PET Characteristics
Chemical Structure
Polyethylene Terephthalate (PET) is another widely used thermoplastic polymer, primarily known for its role in the manufacturing of beverage bottles and synthetic fibers. It is made from the polymerization of ethylene glycol and terephthalic acid, giving it the formula (C10H8O4)n. This chemical makeup is crucial for PET’s excellent barrier properties against oxygen and carbon dioxide, making it ideal for packaging.
Physical Properties
PET is praised for its:
- Strength and Dimensional Stability: PET exhibits good resistance to impact, which prevents it from shattering easily.
- Clarity: It remains transparent; a necessary trait for packaging applications where product visibility is desired.
- Thermal Stability: PET has a higher temperature resistance than many other plastics, which helps in applications involving heat sterilization.
Production Processes
Manufacturing PP
Key Raw Materials
The primary raw material for producing PP is propylene, a byproduct of oil refining and natural gas processing. This availability makes PP a cost-effective material in large-scale production.
Process Description
The production of PP typically involves the following steps:
- Propylene Polymerization: Propylene gas is subjected to a polymerization process using a catalyst system under controlled conditions.
- Pellet Formation: The polymer is then extruded and cut into small pellets that serve as the raw material for various manufacturing processes.
Manufacturing PET
Key Raw Materials
PET production starts with two main ingredients: ethylene glycol and terephthalic acid, both derived from petroleum sources.
Process Description
Manufacturing PET involves:
- Esterification Reaction: Mixing ethylene glycol and terephthalic acid to form a monomer called bis(2-hydroxyethyl) terephthalate.
- Polymerization: The monomer molecules bond together to form long polymer chains through a process called polycondensation, resulting in PET.
Common Uses
Uses of PP
Consumer Goods
- Food Containers: Due to its high melting point and safety, PP is widely used in containers for yogurts, syrups, and ketchup.
- Medical Components: Syringes and vials made from PP are common because it does not react with liquids and is autoclavable.
Industrial Applications
- Automotive Parts: Battery cases and bumpers are often made from PP because of its toughness and resistance to various chemical solvents.
- Construction Materials: PP is used in plastic pipes, ducts, and sheets due to its resistance to degradation and environmental stress.
Uses of PET
Packaging Solutions
- Beverage Bottles: Soft drinks, water, and beer are commonly packaged in PET bottles because they are lightweight, strong, and recyclable.
- Food Packaging: PET is used for packaging salads, fruits, and ready-to-eat meals because it is food-safe and can be sealed airtight.
Textile Fibers
- Clothing: PET fibers are processed into polyester, which is used to make clothing because of its durability and resistance to shrinking and stretching.
Environmental Impact
PP and the Environment
Recyclability
- Sorting and Processing: PP can be recycled after use, although its recycling rates are lower than PET. The process involves sorting, cleaning, melting, and remolding into new products.
Environmental Concerns
- Waste Management: A significant portion of PP waste ends up in landfills due to inadequate recycling processes and facilities. Efforts to improve PP recycling are ongoing to reduce this waste.
PET and the Environment
Recyclability
- High Recyclability: PET is one of the most recycled plastics in the world. Recycled PET (rPET) is used to make everything from new bottles to polyester fibers for the textile industry.
Environmental Benefits
- Reduction in Pollution: Recycling PET significantly reduces plastic pollution and the environmental footprint associated with plastic production. It also conserves resources and energy compared to producing new PET.
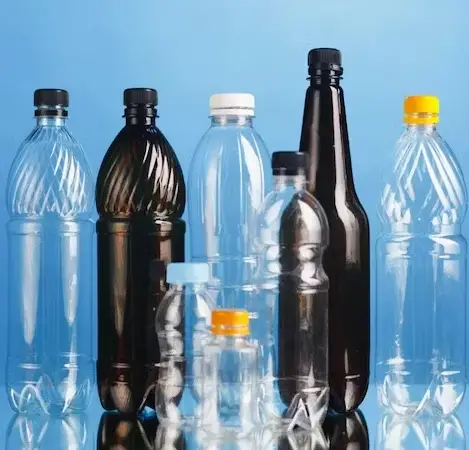
Health and Safety
PP Safety Features
Chemical Resistance
Polypropylene is highly resistant to a broad spectrum of chemicals including acids, bases, and organic solvents. This makes it a safe choice for containers and piping used in laboratories and industrial settings, where exposure to such chemicals is frequent.
Health Considerations
Polypropylene is generally regarded as a safe plastic for human use. It does not leach harmful chemicals into food or drinks, unlike some other plastics. This has led to its widespread use in food packaging and medical products that require sterility and safety:
- Medical Devices: PP is used in medical devices that are in contact with tissues and biological fluids due to its non-reactive nature.
- Food Packaging: Its inertness makes it suitable for containers that store food items over extended periods without altering taste or health safety.
PET Safety Features
Food Safety
PET’s composition makes it ideal for food and beverage packaging. It is:
- FDA Approved: PET meets rigorous health and safety standards and is approved by the Food and Drug Administration for contact with food and beverages.
- Non-Toxic: It does not release harmful substances under normal usage conditions.
Chemical Leaching
While PET is generally safe, under certain conditions, such as high temperatures, it can leach substances like antimony, a catalyst used in its production. However, the levels detected are below those considered harmful by health safety standards.
- Antimony Levels: Research indicates that the levels of antimony leaching from PET bottles are significantly lower than the drinking water standards prescribed by the EPA.
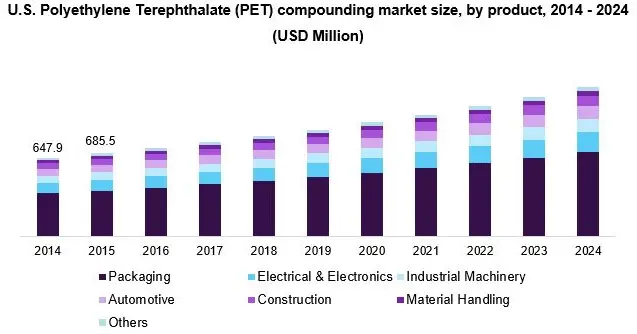
Cost Comparison
Cost Analysis of PP
Production Costs
The production of polypropylene is relatively economical, which is reflected in its widespread use. Factors affecting its cost include:
- Raw Material Availability: Propylene is readily available as a byproduct of oil refining, which helps in keeping the costs down.
- Manufacturing Efficiency: Advances in catalyst technologies have made PP production more efficient over time.
Market Trends
PP prices are influenced by global petroleum prices as it is derived from hydrocarbons. Recently, there has been a trend towards stabilizing prices due to improved production techniques and increased recycling efforts.
- Recycling Impact: Enhanced recycling processes have begun to affect raw material costs, potentially lowering them as more recycled PP enters the market.
Cost Analysis of PET
Production Costs
Producing PET is also cost-effective, particularly because of its high yield and the efficiency of the polycondensation process. Key factors include:
- Scale of Production: Large-scale production has driven down per-unit costs significantly.
- Technological Advances: Innovations in production technology have reduced energy consumption and raw material waste.
Market Trends
The demand for PET, especially recycled PET, has been rising due to its favorable properties and recycling capabilities. This has generally kept prices stable, even with fluctuations in raw material costs:
- Environmental Regulations: Increasing regulations regarding single-use plastics have boosted the recycling market and affected PET pricing positively.
Future Trends
Innovations in PP
Recent Developments
Researchers are constantly working on enhancing the properties of PP to expand its applications. Recent innovations include:
- Improved Barrier Properties: New additives are being developed to enhance PP’s barrier properties against moisture and oxygen.
- Bio-based PP: Efforts are underway to produce polypropylene from renewable sources, which can significantly reduce its environmental footprint.
Future Applications
Future applications of PP aim to replace materials that are less environmentally friendly or less efficient. For example:
- Automotive Industry: New types of PP composites are being designed to replace heavier materials, which helps in reducing vehicle weight and improving fuel efficiency.
Innovations in PET
Recent Developments
Innovations in PET technology focus on enhancing its recyclability and reducing its manufacturing impact on the environment. Some notable developments include:
- Chemical Recycling: Techniques are being refined to break down PET into its monomers, which can then be re-polymerized, offering a purer recycling path.
- Enhanced Processing Techniques: New catalysts and polymerization methods are making the production of PET even more efficient and less costly.
Future Applications
PET is set to expand its role in sustainable practices. Upcoming applications involve:
- Eco-friendly Packaging: With the push towards sustainability, PET’s role in developing fully recyclable and biodegradable forms of packaging is increasing.
- Textile Innovation: Recycled PET is becoming a popular choice for producing eco-friendly fabrics that offer the same quality as virgin materials.
Frequently Asked Questions
What is Polypropylene?
Polypropylene, or PP, is a thermoplastic polymer used extensively in both consumer goods and industrial applications. It is known for its versatility, chemical resistance, and ability to be modified easily, making it suitable for a wide range of products including automotive parts, textiles, and various types of containers.
What is Polyethylene Terephthalate?
Polyethylene Terephthalate, commonly known as PET, is a durable and recyclable plastic predominantly used in the production of packaging materials such as bottles and food containers. It is favored for its strength, thermo-stability, and clarity, which are essential for maintaining the safety and integrity of the packaged goods.
How are PP and PET recycled?
PP and PET can both be recycled, but the process and efficiency differ. PET is one of the most recycled plastics, often turned back into bottles or engineered into polyester fibers for the textile industry. PP recycling is less common due to its lower density and the complexities involved in the process, but it is gaining traction as technology and facilities improve.
Why choose PET over PP?
Choosing between PET and PP depends on the application’s specific requirements. PET is typically chosen for its clarity, barrier properties, and strength, making it ideal for beverage bottles and food packaging. PP is preferred where flexibility, higher temperature resistance, and fatigue resistance are needed, such as in automotive parts and reusable containers.
Conclusion
Polypropylene and Polyethylene Terephthalate are staples in the production of a myriad of plastic products, each serving distinct roles driven by their unique properties. The decision to use PP or PET depends largely on the specific needs of the product being developed, such as durability, flexibility, and environmental impact considerations.
As the global push for sustainable materials continues, understanding the characteristics and recyclability of materials like PP and PET is crucial. This knowledge ensures that manufacturers and consumers make informed choices that align with environmental sustainability and practical functionality.