Silicone-based materials have revolutionized numerous industries with their unique properties and diverse applications. From the automotive sector to personal care products, the versatility of silicones such as polysiloxane and polydimethylsiloxane is evident. These compounds exhibit remarkable chemical stability and can be tailored to meet specific needs, making them invaluable in modern manufacturing and product design.
Polysiloxane and polydimethylsiloxane are two types of silicones distinguished mainly by their chemical structures and resultant properties. Polysiloxane refers to a broader class of polymers containing silicon-oxygen backbone with various organic groups attached, while polydimethylsiloxane is a specific type of polysiloxane where methyl groups are attached to the silicon atoms. This slight variation leads to differences in their physical properties, applications, and performance.
The significance of these materials lies in their ability to perform under challenging conditions. Polysiloxanes are noted for their excellent thermal stability and chemical resistance, which are crucial in high-temperature environments. On the other hand, polydimethylsiloxane stands out for its exceptional lubricating properties and flexibility, making it ideal for medical devices and skincare products.
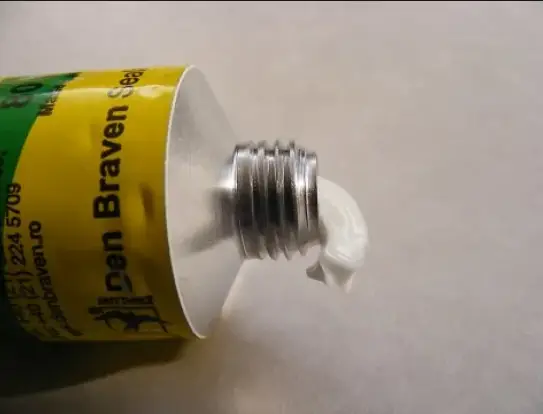
Basic Chemistry
Definition of Polysiloxane
Polysiloxane refers to a class of polymers made primarily from a backbone of alternating silicon and oxygen atoms. This silicon-oxygen chain can be modified by attaching various types of organic groups (R) to the silicon, which affects the material’s properties. Commonly used in a wide range of applications, polysiloxanes are appreciated for their flexibility, durability, and resistance to extreme environments.
Definition of Polydimethylsiloxane
Polydimethylsiloxane (PDMS), often referred to simply as dimethicone, is a specific type of polysiloxane. In PDMS, the organic groups attached to the silicon are exclusively methyl groups (-CH3). This composition makes PDMS notably soft, clear, and non-reactive, which are desirable traits in many consumer products such as lubricants, adhesives, and personal care items.
Chemical Structure Comparison
While both polysiloxane and polydimethylsiloxane share a basic silicon-oxygen backbone, the nature of the organic side groups in polysiloxane can vary greatly, unlike the consistent methyl groups found in PDMS. This variation in side groups can lead to:
- Different physical and chemical properties.
- Alterations in flexibility, thermal stability, and chemical resistance.
Physical Properties
Viscosity Variations
The viscosity of these silicones can vary significantly based on the polymer chain length and the type of side groups attached:
- Shorter chains typically result in lower viscosity, more fluid substances.
- Longer chains and more bulky side groups contribute to higher viscosity, resulting in thicker, gel-like forms.
Thermal Stability
Polysiloxanes are known for their excellent thermal stability, maintaining integrity under high heat, which is crucial in automotive and aerospace applications. PDMS, in particular, does not degrade until exposed to temperatures well above 200°C, making it ideal for products exposed to high heat.
Mechanical Properties
The mechanical properties of these materials are also influenced by their molecular structure:
- Polysiloxanes can range from soft and flexible to hard and rigid, depending on the cross-linking of the polymer chains.
- PDMS is typically soft and very flexible, which is beneficial for applications requiring a material that can conform to varying shapes and maintain a smooth surface.
Manufacturing Processes
Synthesis of Polysiloxane
The production of polysiloxane involves several key steps:
- Base polymerization: Monomers with silicon and oxygen are polymerized to form a base polysiloxane structure.
- Chain branching and cross-linking: Depending on the intended use, the polymer may be further modified to change its structure and properties.
Synthesis of Polydimethylsiloxane
Producing PDMS follows a similar initial path but focuses on maintaining the consistency of using methyl groups:
- Polymerization: Specific catalysts are used to encourage the linking of monomers that exclusively include methyl groups attached to silicon.
- Curing: After polymerization, the material is cured to achieve the desired mechanical and physical properties.
Key Differences in Production
The key differences in the production processes of these materials largely revolve around the types of catalysts used and the specific conditions under which polymerization and curing occur, affecting the end product’s properties and applications.
Common Applications
Use in Coatings
Polysiloxane coatings are valued for their ability to provide durable, weather-resistant protective layers on buildings and vehicles. These coatings are especially effective in preventing corrosion and wear in harsh environmental conditions.
Role in Sealants and Adhesives
Both materials are excellent choices for sealants and adhesives due to their flexibility, waterproof properties, and strong bonding capabilities. PDMS is particularly used in situations where a clear, non-staining adhesive is required, such as in glass and bath applications.
Medical and Cosmetic Applications
PDMS stands out in medical and cosmetic applications due to its non-toxic and skin-friendly properties. It is commonly found in items ranging from contact lenses and medical devices to skin moisturizers and hair conditioners, where it provides a smooth, protective, and non-irritating layer.
Performance in Industries
Automotive Uses
In the automotive industry, both polysiloxane and polydimethylsiloxane are crucial for enhancing the performance and durability of vehicle components. Their applications include:
- Sealants: Provide durable seals that withstand high temperatures and chemical exposure, crucial for engine and transmission parts.
- Insulation: Used in electrical wiring and sensors due to their excellent electrical insulation properties.
- Vibration damping: Help reduce noise and absorb vibrations, improving vehicle comfort and performance.
The use of these materials helps extend the lifespan of automotive parts, contributing to more reliable and longer-lasting vehicles.
Electronics and Electrical
Silicones play a pivotal role in the electronics industry due to their electrical insulative properties and thermal stability. Key applications include:
- Protective coatings: Guard sensitive electronic components against moisture, dust, and extreme temperatures.
- Encapsulants: Encase electronic assemblies to protect against mechanical stress and environmental factors.
- Thermal management: Used in applications requiring heat dissipation from electronic components to prevent overheating.
These properties ensure that devices operate safely and efficiently, even under harsh conditions.
Building and Construction
Polysiloxane and polydimethylsiloxane are extensively used in the construction industry due to their flexibility, durability, and resistance to weathering. Their primary uses include:
- Waterproof coatings: Protect buildings from water damage and reduce maintenance costs.
- Joint sealants: Provide flexibility and prevent cracks in building materials due to temperature changes.
- Glazing seals: Enhance the insulation properties of glass installations, improving energy efficiency.
Their ability to withstand environmental factors makes them ideal for modern construction needs, enhancing building longevity and reducing upkeep.
Environmental Impact
Biodegradability and Environmental Safety
Although silicones are generally stable and inert, concerns about their environmental impact have prompted research into their biodegradability and potential effects on ecosystems. Key findings include:
- Low biodegradability: Silicones are not readily biodegradable, which means they persist in the environment.
- Minimal toxicity: Studies show that silicones have low toxicity levels for aquatic and terrestrial life.
Despite their stability, ongoing studies aim to fully understand their environmental lifecycle and develop more sustainable disposal methods.
Regulations and Compliance
As the use of silicones has grown, so has the regulatory landscape governing their manufacture and use. Compliance with environmental regulations is crucial for manufacturers, with standards focusing on:
- Emissions: Controlling the release of volatile organic compounds during manufacturing.
- Waste management: Proper handling and disposal of silicone waste to minimize environmental impact.
- Product safety: Ensuring that silicone products are safe for use, particularly in sensitive applications like food contact materials and medical devices.
Manufacturers must stay informed about these regulations to not only ensure compliance but also to maintain their market position and public trust.
Future Trends
Innovations in Silicone Technology
The future of silicone technology looks promising with several innovations on the horizon. Researchers are exploring ways to enhance the properties of silicones, such as:
- Improved biodegradability: Developing silicones that break down more readily in the environment.
- Enhanced performance: Creating silicones with even greater thermal stability and mechanical properties for advanced engineering applications.
These advancements are expected to open new markets and applications for silicones, from biomedicine to aerospace.
Potential Growth Sectors
Anticipated growth sectors for silicones include:
- Renewable energy: Use in solar panels and wind turbines for weatherproofing and efficiency enhancement.
- Electric vehicles: Demand for high-performance, durable silicones in batteries and electronic components.
- Healthcare: Expanded use in medical implants and devices, benefiting from silicones’ biocompatibility and stability.
Frequently Asked Questions
What is Polysiloxane?
Polysiloxane is a type of silicone polymer known for its robust silicon-oxygen backbone, which can be modified with various organic groups to enhance its properties. It is widely used in applications requiring high thermal stability and chemical resistance, such as protective coatings and electrical insulations.
How is Polydimethylsiloxane used?
Polydimethylsiloxane, commonly abbreviated as PDMS, is utilized primarily for its excellent lubricating properties and flexibility. It finds extensive use in medical devices, skin and hair care products, and in the creation of silicone molds due to its non-toxic and hypoallergenic nature.
Are Polysiloxane and Polydimethylsiloxane environmentally safe?
Both polysiloxane and polydimethylsiloxane are considered to be environmentally safe materials due to their inert nature and resistance to degradation under normal environmental conditions. They do not leach harmful chemicals and are used in various eco-friendly applications.
What are the main differences between Polysiloxane and Polydimethylsiloxane?
The main differences between these two silicones lie in their chemical structures and physical properties. Polysiloxane has a variable organic group attachment, offering diverse properties, while polydimethylsiloxane specifically features methyl groups, contributing to its flexibility and moisture resistance.
Conclusion
The distinctions between polysiloxane and polydimethylsiloxane highlight the importance of understanding material properties in choosing the right silicone for specific applications. Each type offers unique benefits that can be leveraged in different industries to enhance product performance and durability. As the demand for advanced materials continues to grow, the role of these silicones is expected to expand, driving further innovations and applications.
In conclusion, the informed selection of either polysiloxane or polydimethylsiloxane can significantly impact the efficiency and effectiveness of products across various sectors. Recognizing their capabilities and limitations not only aids in better material selection but also fosters innovation in product development and design.