The Oxo and Wacker processes stand as pillars in the realm of industrial chemistry, each playing a pivotal role in synthesizing crucial chemicals that fuel various sectors of the modern world. These processes, though different in approach and outcome, represent the ingenuity of chemical engineering and its capacity to drive industrial advancements. By transforming simple molecules into more complex, valuable compounds, they underscore the essence of chemical synthesis in industrial applications.
The Oxo process primarily converts olefins into aldehydes through hydroformylation, utilizing specific catalysts, whereas the Wacker process involves the oxidation of ethylene to produce acetaldehyde, employing palladium as a catalyst. Both processes are instrumental in producing a range of chemicals that serve as foundational building blocks in the manufacturing of plastics, solvents, and other significant industrial products.
Delving deeper, these processes not only differ in the chemical reactions and catalysts involved but also in their environmental impacts, efficiency, and the specific industrial applications they cater to. The Oxo process is renowned for its versatility in producing various aldehydes, which are further processed into alcohols and acids, while the Wacker process is pivotal in generating acetaldehyde, a precursor for numerous synthetic chemicals. Understanding these distinctions is essential for industries aiming to optimize their chemical synthesis routes, balance environmental considerations, and meet the evolving demands of the market.
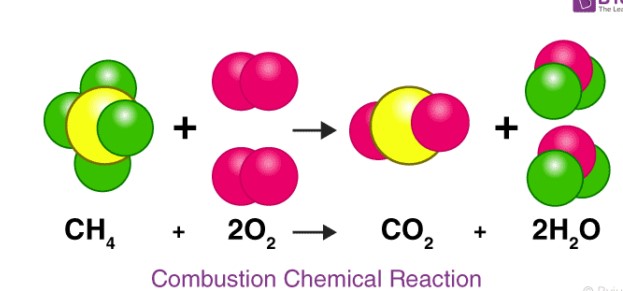
Oxo Process Explained
Definition and Basics
The Oxo Process, also known as hydroformylation, is a crucial chemical reaction in the industrial sector. It involves the conversion of olefins (unsaturated compounds) into aldehydes through the addition of synthesis gas (a mixture of hydrogen and carbon monoxide) in the presence of a catalyst. This process is fundamental in creating intermediates for various commercial products.
Historical Background
The discovery of the Oxo Process dates back to the 1930s, marking a significant advancement in organic chemistry. Developed by chemists at Ruhr Chemie AG in Germany, this method opened new pathways in synthesizing alcohols and acids from olefins, which were abundantly available. Over the decades, it has been refined, leading to more efficient and environmentally friendly catalyst systems.
Chemical Reaction and Catalysts
The core of the Oxo Process is the catalytic reaction that transforms olefins into aldehydes. This involves:
- Reaction: Olefin + H₂ + CO → Aldehyde
- Catalysts: Typically, cobalt or rhodium complexes, with rhodium being more effective for lower-alkene substrates due to its selectivity and control.
The choice of catalyst significantly affects the efficiency, rate, and selectivity of the reaction, making ongoing research into catalyst development a critical aspect of optimizing the Oxo Process.
Key Applications and Products
The products of the Oxo Process, primarily aldehydes, serve as precursors for a wide range of chemicals. These include:
- Alcohols: By further hydrogenation of aldehydes.
- Acids: Through oxidation of aldehydes.
- These intermediates are foundational in producing plastics, solvents, and pharmaceuticals.
Wacker Process Overview
Definition and Introduction
The Wacker Process is another pivotal chemical reaction in industry, focusing on the oxidation of ethylene to produce acetaldehyde. Utilizing a palladium catalyst, this process exemplifies a practical application of catalytic oxidation in creating valuable chemical products.
Development and Historical Significance
First commercialized in the 1950s by the Wacker Chemie AG, this process represented a significant breakthrough in the production of acetaldehyde, a key industrial chemical. The Wacker Process offered a more efficient and less energy-intensive method compared to prior techniques, cementing its role in chemical manufacturing history.
Chemical Mechanism and Catalysts Involved
The Wacker Process involves:
- Reaction: Ethylene + ½ O₂ → Acetaldehyde
- Catalysts: A system of palladium (II) chloride and copper (II) chloride, which acts synergistically to oxidize ethylene effectively.
The choice of catalysts here is crucial for the reaction’s speed and yield, highlighting the importance of catalyst research in this area as well.
Main Applications and Industrial Importance
Acetaldehyde, the primary product of the Wacker Process, is used extensively in:
- Synthesis of acetic acid and its derivatives.
- Manufacturing of perfumes, flavors, and pharmaceuticals.
Its wide range of applications demonstrates the Wacker Process’s central role in the chemical industry.
Core Differences
Chemical Reactions
- Oxo Process: Converts olefins into aldehydes.
- Wacker Process: Oxidizes ethylene to acetaldehyde.
These reactions highlight the distinct goals and products of each process.
Catalysts Used
- Oxo Process: Utilizes cobalt or rhodium complexes.
- Wacker Process: Employs a palladium and copper chloride system.
The choice of catalyst is pivotal in defining each process’s efficiency and selectivity.
End Products
- Oxo Process: Produces aldehydes as intermediates for further chemical synthesis.
- Wacker Process: Directly produces acetaldehyde, a valuable chemical precursor.
Industrial Applications
- Oxo Process: Broadly used in manufacturing plastics and solvents.
- Wacker Process: Essential for producing acetic acid and derivatives.
Environmental Impact
The environmental footprint of each process varies based on:
- Emissions: Chemical processes produce byproducts and emissions, with ongoing research aimed at minimizing these impacts.
- Resource Use: Catalysts and energy requirements differ, affecting their sustainability.
Chemical Reactions Compared
Oxo Process Reaction Specifics
The Oxo Process’s hydroformylation reaction involves complex kinetics and is influenced by the nature of the olefin and the catalyst system used. The efficiency and selectivity toward the desired aldehyde product are critical considerations.
Wacker Process Reaction Details
In the Wacker Process, the oxidation of ethylene is a more straightforward reaction but requires a delicate balance of catalysts to ensure high yield and minimize byproducts.
Comparative Analysis
While both processes transform simple molecules into more complex and industrially valuable products, their mechanisms, catalysts, and outcomes differ significantly. This comparison highlights the diversity in chemical manufacturing techniques and their optimization for specific end products.
Catalysts Role
Catalysts in Oxo Process
Cobalt and rhodium catalysts in the Oxo Process have been studied extensively for their roles in improving reaction rates and selectivity towards specific aldehydes. Rhodium, in particular, offers superior control, especially for lower-alkene substrates.
Catalysts in Wacker Process
The palladium-copper system in the Wacker Process is notable for its ability to efficiently oxidize ethylene to acetaldehyde, with research focused on reducing catalyst degradation and optimizing the reaction environment.
Comparison and Significance
The choice and development of catalysts in both processes are central to their industrial viability and environmental impact. Innovations in catalyst technology continue to enhance these processes, aiming for higher efficiency, lower costs, and reduced environmental footprints.
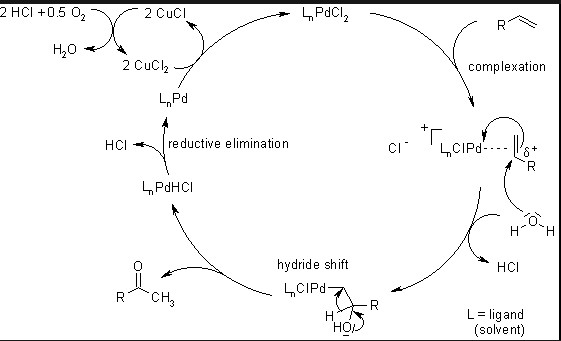
Products and Applications
Oxo Process Products
The Oxo Process is renowned for its versatility in producing a wide range of chemical intermediates and products. Central to its output are aldehydes, which undergo further reactions to yield:
- Alcohols: These are obtained by hydrogenating the aldehydes produced. Alcohols are pivotal in the manufacturing of plasticizers, detergents, and solvents.
- Acids: Oxidation of aldehydes leads to acids, used in making esters for perfumes and flavorings, as well as in the production of plasticizers.
These products are foundational in creating materials that are integral to our daily lives, from the plastic components in electronics to the fragrances in personal care products.
Wacker Process Products
The Wacker Process mainly produces acetaldehyde, a key intermediate in chemical synthesis. Acetaldehyde serves as a precursor for:
- Acetic Acid: A vital industrial chemical used in making vinegar, as well as in the production of synthetic fibers and plastics.
- Ethyl Acetate: A solvent used in paints, varnishes, and the coffee decaffeination process.
- Peracetic Acid: A disinfectant and sterilizer.
These applications underscore the critical role of acetaldehyde in various sectors, including food, healthcare, and manufacturing.
Sector-wise Applications Comparison
The Oxo Process finds its applications spread across multiple sectors, from automotive, where alcohols produced are used in brake fluids, to construction, where plasticizers derived from alcohols and acids are employed in making flexible PVC.
Conversely, the Wacker Process, through its production of acetaldehyde, impacts the food industry by contributing to the synthesis of vinegar, as well as the pharmaceutical and cosmetic sectors through the production of solvents and perfumes.
Environmental Considerations
Emissions and Byproducts
Both processes contribute to industrial emissions and byproducts. The Oxo Process can generate waste in the form of unused gases and catalyst remnants, whereas the Wacker Process is noted for its potential to release chlorine-containing byproducts, which need careful handling and disposal.
Sustainability Aspects of Both Processes
Sustainability efforts for both processes focus on minimizing waste, improving catalyst efficiency, and reducing energy consumption. Innovations in catalyst design and process optimization are key strategies to achieve these goals.
Advances in Minimizing Environmental Impact
Recent advances include:
- Recycling of catalysts in both processes to reduce waste and costs.
- Process optimization to lower energy requirements and enhance reaction efficiency.
- Development of green catalysts, particularly for the Oxo Process, to lessen environmental impact.
Technological Advancements
Recent Innovations in Oxo Process
Technological advancements in the Oxo Process have led to:
- The introduction of rhodium-based catalysts with higher selectivity, reducing byproduct formation.
- Process intensification techniques, such as microreactor technology, enhancing reaction rates and efficiency.
Wacker Process Modern Improvements
For the Wacker Process, innovations include:
- The development of membrane cell technology for more efficient palladium recovery and reuse.
- Catalyst regeneration techniques, minimizing the loss of palladium and reducing operational costs.
Impact on Efficiency and Sustainability
These technological advancements not only improve the economic viability of the Oxo and Wacker processes but also enhance their sustainability by reducing energy consumption, minimizing waste, and lowering greenhouse gas emissions.
Economic Aspects
Cost-effectiveness Comparison
The cost-effectiveness of both processes is influenced by raw material prices, catalyst costs, and energy requirements. The Oxo Process generally involves higher catalyst costs due to the use of expensive metals like rhodium, but its broad range of products can offset these expenses. The Wacker Process, while more specific in its product range, benefits from catalyst recycling and regeneration techniques that keep operational costs in check.
Market Demand for Products
Market demand for the products of both processes remains strong. For the Oxo Process, the growing automotive and construction sectors drive demand for alcohols and acids. In contrast, the Wacker Process benefits from steady demand in the food, pharmaceutical, and cosmetic industries for acetaldehyde and its derivatives.
Future Prospects in Chemical Industry
The future of both the Oxo and Wacker processes looks promising, with ongoing research into catalyst efficiency, process optimization, and environmental sustainability poised to expand their applications and reduce their environmental footprints. The adaptability of these processes to meet changing market demands and environmental standards ensures their continued relevance and growth in the chemical industry.
Frequently Asked Questions
What is the Oxo Process?
The Oxo process, also known as hydroformylation, is a catalytic process that converts olefins into aldehydes using synthesis gas (a mixture of hydrogen and carbon monoxide) in the presence of a metal catalyst. This process is vital for producing intermediates used in manufacturing plastics, detergents, and other significant products.
How does the Wacker Process work?
The Wacker process involves the oxidation of ethylene to acetaldehyde in the presence of palladium chloride as a catalyst. This reaction is a key method for acetaldehyde production, essential for synthesizing various chemicals, including acetic acid, perfumes, and solvents.
What are the key differences between the Oxo and Wacker processes?
The primary difference lies in their chemical reactions and the products they yield. The Oxo process focuses on converting olefins into aldehydes, while the Wacker process oxidizes ethylene to produce acetaldehyde. Additionally, their catalysts, environmental impact, and industrial applications vary, reflecting their distinct roles in chemical synthesis.
Why are catalysts important in these processes?
Catalysts are crucial for enhancing the efficiency and selectivity of chemical reactions in both processes. In the Oxo process, catalysts enable the conversion of olefins at lower temperatures and pressures. Similarly, in the Wacker process, catalysts facilitate the efficient oxidation of ethylene to acetaldehyde, making these reactions commercially viable.
Conclusion
The Oxo and Wacker processes embody the dynamic nature of industrial chemistry, showcasing how fundamental chemical principles can be harnessed to meet industrial needs and challenges. Their distinct methodologies, applications, and impacts on the chemical industry highlight the importance of understanding and optimizing these processes. As the industry evolves, the continuous improvement and adaptation of these processes will be paramount in addressing environmental concerns and enhancing production efficiency.
In sum, the comparison between the Oxo and Wacker processes provides invaluable insights into the complexities of chemical synthesis in industrial applications. It underscores the necessity of innovation, sustainability, and strategic planning in the chemical industry’s future development. Through such understanding, industries can better navigate the intricacies of chemical processes, paving the way for advancements that align with both economic and environmental goals.