Metal melting is a fundamental aspect of industrial manufacturing, involving various methods to convert raw metallic inputs into usable forms. Two prominent methods are crucible melting and cupola operation, each with distinct procedures and outcomes. By examining the specifics of these techniques, industries can better decide which method suits their needs based on factors like purity, cost, and environmental impact.
Crucible melting involves heating metal in a refractory container until it melts, which is then poured into molds to solidify. This method is known for producing high-purity metals, making it ideal for applications where material quality is paramount. On the other hand, cupola operation uses a shaft furnace where layers of metal, coke, and limestone are melted together, primarily for cast iron production. It stands out for its cost efficiency and high production capacity.
While crucible melting offers precise temperature control and purity, it is limited by smaller batch sizes and higher energy costs. Conversely, cupola furnaces excel in continuous high-volume production but may compromise on the metal’s purity and have significant environmental implications due to higher emissions. Choosing between these methods depends largely on the specific needs and constraints of the production process.
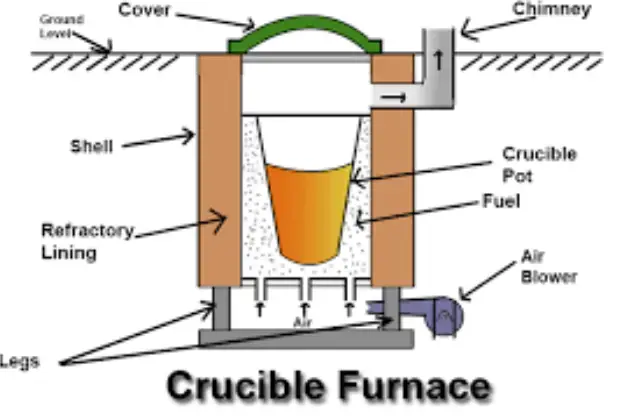
Crucible Melting
Basics of Crucible Melting
Definition and Process Description
Crucible melting is a technique in which metal is melted in a heat-resistant container known as a crucible. The process involves heating the crucible to temperatures high enough to melt the contained metal, typically using sources such as electrical, gas, or induction heating. The melted metal can then be poured into molds to create various metal products.
Types of Crucibles Used
There are several types of crucibles used in this melting method, each suited for different metals and melting environments:
- Graphite Crucibles: Highly durable and excellent for high-temperature melting of metals like copper and aluminum.
- Silicon Carbide Crucibles: Preferred for higher temperature alloys and iron due to their thermal conductivity and shock resistance.
- Ceramic Crucibles: Best for precious metals like gold and silver as they prevent contamination.
Advantages of Crucible Melting
Purity of Output
The primary advantage of crucible melting is the purity of the metal produced. Since the metal does not contact any other materials but the crucible, contamination is significantly minimized. This purity is crucial for applications requiring high-grade metals with predictable properties.
Control Over Melting Temperature
Crucible melting allows for precise control over the melting temperature, which is vital for metals that have narrow melting ranges. This control ensures that the metal properties remain consistent and predictable, essential for quality manufacturing.
Disadvantages of Crucible Melting
Limited Capacity
One of the significant drawbacks of crucible melting is its limited capacity. Crucibles can only hold a certain amount of metal, which restricts the volume of metal that can be processed at a time. This limitation makes crucible melting less suitable for large-scale production.
Energy Consumption
The energy consumption of crucible melting is relatively high. Heating a crucible to the required temperatures to melt metals can be energy-intensive, especially for high-melting-point metals, making this process less energy efficient compared to others.
Applications of Crucible Melting
Industries Using Crucible Melting
Crucible melting is predominantly used in industries where metal purity is paramount, such as:
- Jewelry making
- Aerospace components
- Electronic parts manufacturing
Common Metals Processed
Metals typically melted in crucibles include:
- Gold
- Silver
- Copper
- Aluminum
Cupola Operation
Basics of Cupola Operation
Definition and Operational Mechanics
A cupola furnace is a tall, vertical furnace used primarily for melting iron and iron alloys. It operates continuously with materials charged at the top and molten metal and slag tapped out at the bottom. Air is blown into the furnace through tuyeres to facilitate combustion and maintain temperature.
Components of a Cupola Furnace
Key components of a cupola furnace include:
- Shell: Made of steel, lined with refractory material to withstand high temperatures.
- Charging door: Where materials are added.
- Tuyeres: Openings through which air is injected.
- Hearth: Where molten metal collects and is tapped out.
Advantages of Cupola Operation
High Production Rate
Cupola furnaces are capable of melting large amounts of metal quickly, making them suitable for high-volume production needs.
Cost-effectiveness
Due to the continuous nature of the operation and the ability to use lower cost fuels like coke, cupola operation is a cost-effective method of producing large quantities of cast iron.
Disadvantages of Cupola Operation
Lower Metal Purity
The metal produced in a cupola furnace generally has lower purity compared to crucible melting. The interaction with coke and the potential for contamination from other materials charged into the furnace can affect the metal’s properties.
Environmental Concerns
Cupola furnaces emit a range of pollutants, including particulates, sulfur dioxide, and other harmful gases, posing significant environmental and health risks.
Applications of Cupola Operation
Predominant Industries
Industries that rely on cupola furnaces include:
- Foundries for casting iron
- Automotive parts manufacturers
Range of Materials Processed
Materials commonly processed in cupola furnaces include:
- Cast iron
- Recycled iron scrap
This detailed examination of crucible melting and cupola operation showcases the distinct features, advantages, and drawbacks of each method, helping industries to choose the most suitable approach based on their specific requirements.
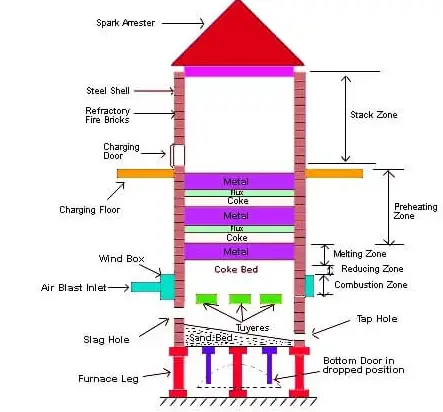
Comparative Analysis
Efficiency Comparison
Energy Usage and Sustainability
When comparing the energy efficiency of crucible melting and cupola operation, crucible melting tends to be less energy efficient due to the high temperatures needed for smaller batches. Each batch requires a significant amount of energy to reach melting points, leading to higher overall energy consumption per unit of metal.
Cupola furnaces, on the other hand, can continuously melt large amounts of metal, dispersing energy costs over a greater output, thus enhancing overall energy efficiency. However, the sustainability of each method varies significantly. Crucible melting, using cleaner energy sources like electricity, can be seen as more sustainable, especially when renewable energy sources are implemented.
Output Rate Analysis
Cupola furnaces excel in terms of output rate, capable of processing thousands of kilograms of iron per hour. This makes them ideal for large-scale industrial operations that require high volumes of metal. Crucible melting is more suited to specialized productions where smaller quantities of high-purity metal are needed.
Quality and Control
Metal Quality from Each Method
The quality of metal from crucible melting is generally higher. This method allows for a controlled environment where impurities can be minimized, resulting in superior metal quality ideal for high-specification applications. In contrast, metal from cupola operations, while satisfactory for many uses, may contain more impurities due to the interaction with coke and the potential for contamination from slag.
Process Control in Melting Operations
Process control is more refined in crucible melting, where temperatures can be precisely adjusted to suit the melting point of specific metals. This precise control helps in maintaining consistent metal properties throughout the batch. Cupola operation, while effective for large-scale production, offers less control over the individual batch quality, leading to variability in the final product.
Cost Implications
Operational Cost Analysis
From a cost perspective, cupola operation tends to be less expensive on a per-unit basis due to its higher throughput and the use of cheaper fuel sources like coke. Crucible melting, though it requires higher energy per unit, justifies its cost with the ability to produce high-quality, specialized metals that can be sold at a premium.
Maintenance and Longevity
Maintenance needs and the longevity of the equipment also differ. Cupola furnaces, while robust, require regular maintenance to manage the intense wear and tear from continuous operation. Crucible furnaces may require less frequent maintenance but can be costly when a replacement is necessary due to the high-quality materials needed for construction.
Environmental Impact
Emissions and Regulations
Cupola furnaces are significant contributors to industrial emissions, releasing large quantities of carbon dioxide and particulates. This has led to stringent regulations requiring the implementation of emission control technologies. Crucible melting produces fewer emissions overall but still faces regulatory scrutiny, particularly in regions with strict environmental laws.
Advances in Eco-Friendly Practices
Both methods have seen advances in eco-friendly practices. Innovations in crucible technology include the use of electric and induction heating to reduce carbon footprints. For cupolas, developments like improved filtration systems and the integration of scrubbers help mitigate environmental impacts.
Future Trends
Technological Advancements
Innovations in Metal Melting
Technological advancements are shaping both crucible melting and cupola operations. New materials for crucibles allow for higher temperature operations with less energy, while advancements in furnace design are increasing the efficiency and environmental friendliness of cupola furnaces.
Impact on Crucible and Cupola Methods
These innovations have a profound impact on the choice and efficiency of metal melting methods. Enhanced refractory materials extend the life of crucibles, reducing replacement costs. For cupolas, better control systems are improving process efficiency and reducing waste.
Industry Adaptations
Changes in Industrial Demand
Changes in industrial demand, driven by sectors like automotive and aerospace, require higher quality and precision metals. This trend favors the growth of crucible melting in sectors where material properties are critical.
Shifts Towards Sustainable Practices
There is a clear shift towards sustainable practices in the metal production industry. Regulatory pressures and environmental concerns are pushing companies to adopt greener technologies and practices. This shift influences both crucible and cupola operations to innovate continuously to meet these new standards.
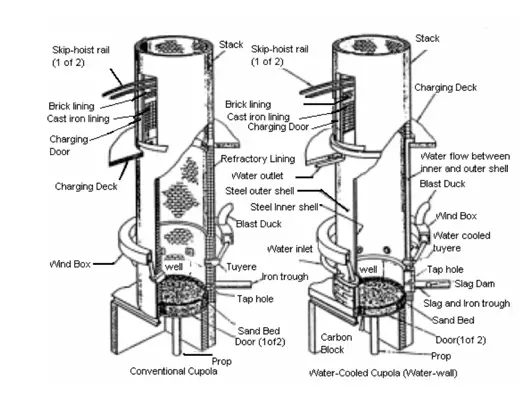
Frequently Asked Questions
What is Crucible Melting?
Crucible melting is a process where metals are melted in a high-temperature resistant container known as a crucible. This method is particularly used for achieving high-purity metals, essential in industries like aerospace and electronics where material integrity is critical.
How Does a Cupola Furnace Work?
A cupola furnace operates through a continuous method where iron, coke, and flux are layered and heated at high temperatures. Air is blown through the shaft to facilitate combustion, making it efficient for melting large quantities of metal, primarily used in the production of cast iron.
What are the Environmental Impacts of Cupola Operation?
Cupola operations, while efficient and cost-effective, pose significant environmental challenges. They emit a considerable amount of particulates, CO2, and other pollutants, necessitating stringent emission controls and modernization to comply with environmental regulations.
Can Crucible Melting Handle Large Productions?
Crucible melting is generally more suited for smaller production scales due to its limited crucible size and higher energy requirements per unit of metal melted. It is ideal for producing high-quality metals in smaller quantities rather than large-scale industrial production.
What Advantages Does Cupola Operation Offer Over Crucible Melting?
Cupola operation offers several advantages over crucible melting, including lower operational costs, higher production capacity, and the ability to melt a wide variety of metals. It is particularly advantageous for industries that require large volumes of cast iron.
Conclusion
In summary, the choice between crucible melting and cupola operation hinges on several factors, including desired metal purity, production volume, cost constraints, and environmental considerations. Crucible melting is preferable when quality and purity are critical, whereas cupola operation is suited for high-volume, cost-sensitive projects.
As industries continue to evolve and environmental regulations become stricter, the future of metal melting may see technological advancements that enhance both methods’ efficiency and sustainability. Understanding these methods’ distinct advantages and limitations helps stakeholders make informed decisions that align with their operational goals and environmental responsibilities.