Surface treatments like coating and plating are integral to various manufacturing processes, offering benefits from aesthetic enhancements to functional improvements in durability and corrosion resistance. These processes are widely applied across industries, each serving distinct purposes based on the material properties and desired outcomes.
Coating involves applying a substance over a material to protect or decorate the surface. Plating, on the other hand, entails depositing a metal onto a conductive surface, enhancing properties such as corrosion resistance, hardness, and electrical conductivity. Both techniques are crucial for extending the lifespan and functionality of products in sectors such as automotive, aerospace, and electronics.
While coatings are typically polymers applied as liquids or powders that cure into a solid, platings are metallic layers achieved through chemical or electrochemical processes. The choice between coating and plating depends on several factors including performance requirements, environmental considerations, and cost constraints, each providing unique benefits and challenges.
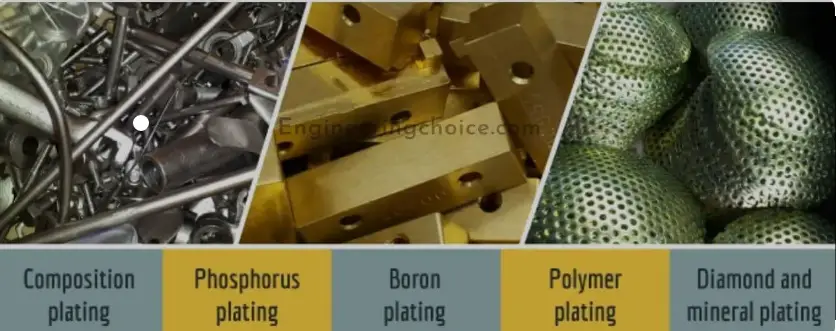
Coating Basics
Definition and Purpose
Coating refers to the application of a protective or decorative layer on a surface. Its primary purpose is to enhance a material’s properties, such as its resistance to corrosion, wear, and tear, and to improve its aesthetic appeal. Coatings are essential in extending the lifespan of various products and are widely used in industries like automotive, construction, and consumer goods.
Types of Coatings
Paint
Paint is one of the most common types of coatings. It consists of pigments suspended in a liquid binder that forms a thin film when applied to a surface. This film protects surfaces from moisture, UV rays, and chemical exposure. Paints are available in various formulas, including water-based, oil-based, and acrylic, each offering distinct benefits and uses.
Powder
Powder coating is a dry finishing process where powdered paint is electrostatically charged and sprayed onto a part. It is then cured under heat to form a skin-like layer that is tougher and more durable than conventional paint. Powder coating is popular for its environmental benefits, as it produces fewer volatile organic compounds (VOCs) and offers a thicker, more uniform coating without running or dripping.
Ceramic
Ceramic coatings are advanced materials that offer high-temperature resistance and exceptional hardness. Made from silicate compounds, these coatings are ideal for applications requiring thermal stability, such as engine components and exhaust systems. Ceramic coatings also provide excellent UV resistance and hydrophobic properties, making surfaces easier to clean.
Plating Fundamentals
What is Plating?
Plating involves the deposition of a metal layer onto a conductive surface. This process enhances the substrate’s properties, including its aesthetic appearance, corrosion resistance, and electrical conductivity. Plating is crucial in manufacturing, electronics, and decorative applications.
Common Plating Metals
Gold
Gold plating is prized for its excellent electrical conductivity and resistance to oxidation. Used extensively in electronics and fine jewelry, gold plating adds both functional and decorative value.
Silver
Silver plating is known for its high electrical conductivity and thermal conductivity, making it ideal for electrical and thermal applications. It is also used in decorative arts for its bright, white metallic finish.
Chrome
Chrome plating not only provides a mirror-like finish but also offers superb hardness and resistance to tarnish. Commonly used in automotive and plumbing fixtures, chrome plating enhances both functionality and style.
Process Comparison
Coating Application Methods
The application of coatings can vary significantly, involving methods such as brushing, spraying, dipping, and flow coating. Each method suits different types of coatings and substrate geometries, impacting the final finish and properties of the coating.
Plating Techniques
Plating can be performed using electroplating or electroless plating techniques. Electroplating uses electrical current to reduce dissolved metal cations so that they form a coherent metal coating on the electrode. Electroless plating, however, involves chemical reduction to achieve plating without the use of electric current.
Material Considerations
Substrates for Coating
The substrates suitable for coating include metals, plastics, ceramics, and even wood. The choice of substrate dictates the type of coating used, as each material interacts differently with various coating compounds.
Substrates for Plating
Primarily, plating is done on metals and conductive surfaces. However, innovations such as conductive paints and treatments have enabled plating on non-traditional substrates like plastics and glass.
Performance Metrics
Durability and Lifespan
Both coating and plating are designed to extend the durability and lifespan of the treated surfaces. The effectiveness of each depends on the correct selection of materials and processes based on the end-use environment.
Aesthetic and Functionality
Aesthetically, coatings and platings can drastically improve a product’s appearance while also adding functional benefits such as improved wear resistance and lower maintenance needs. This dual role is vital in consumer-facing products where appearance can be as important as performance.
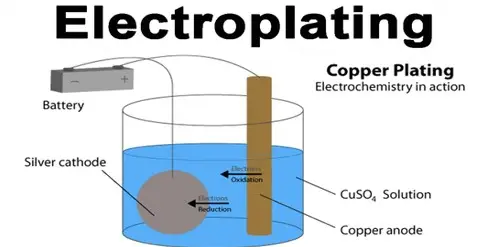
Cost Analysis
Coating Expenses
When evaluating coating expenses, several factors come into play. Material costs, such as for paint, powder, or ceramics, significantly influence the overall expense. Additionally, the complexity of the application process and the need for specialized equipment can raise costs. Economies of scale often apply, with larger production volumes typically reducing the cost per unit.
Plating Expenses
Plating costs are largely determined by the metals used—gold, silver, and chrome are notably more expensive than less precious metals. The electroplating process also requires substantial energy and sophisticated equipment, contributing to higher operational costs. Like coating, volume can affect cost efficiency, making plating more economical at higher quantities.
Environmental Impact
Coating Eco-Friendliness
The environmental impact of coatings varies by type. Water-based paints, for example, are more eco-friendly than solvent-based options because they emit lower levels of VOCs. Powder coatings also represent a greener choice as they produce minimal waste and volatile compounds.
Plating and Pollution
Plating can pose significant environmental challenges, especially when involving toxic metals like chromium or nickel. The process can produce hazardous waste and air pollutants. Regulations such as the EPA’s standards aim to control and minimize the impact of these substances on the environment.
Industry Applications
Automotive Uses
In the automotive industry, both coatings and platings are essential for both protection and aesthetics. Coatings are used extensively for body paint, undercoating for rust prevention, and interior varnishes. Platings are critical in components that require durability and corrosion resistance, such as engine parts and exterior trim.
Electronics Field
The electronics industry relies heavily on plating for circuit boards and connectors, using metals like gold and silver to ensure good electrical conductivity and resistance to corrosion. Coatings are applied to casings and parts to prevent damage and extend the life of the devices.
Advances and Innovations
Latest in Coating Technologies
Recent innovations in coating technologies include the development of nano-coatings and smart coatings that change properties in response to environmental stimuli. These advancements offer improved performance in extreme conditions and new functionalities, like self-healing or color-changing capabilities.
New Trends in Plating
In plating, recent trends focus on sustainability and efficiency. Innovations such as trivalent chromium plating provide alternatives to hexavalent chromium, offering similar quality without the environmental and health risks traditionally associated with chromium finishes.
Choosing Between Coating and Plating
Factors to Consider
Choosing the right surface treatment requires consideration of several factors:
- Material compatibility: Certain materials can only be coated or plated with specific substances.
- Desired properties: Depending on whether the priority is aesthetic appeal, durability, or corrosion resistance, one method may be more suitable than the other.
- Environmental impact: Eco-friendly options may be necessary based on industry regulations or corporate sustainability goals.
Decision-making Criteria
The decision-making process often involves a cost-benefit analysis, weighing the long-term benefits of durability and maintenance against the initial costs. For sectors like automotive or electronics, where performance and reliability are paramount, the choice may lean towards more robust solutions, despite higher upfront costs.
Frequently Asked Questions
What is surface coating?
Surface coating refers to the application of a liquid or powdered material to a surface, which then cures or sets to form a protective or decorative layer. This process is used to enhance appearance, resistance to wear, corrosion, and other environmental factors.
How does plating differ from coating?
Plating involves the deposition of a metal onto a conductive surface, usually through electrochemical means. It is primarily used to improve a substrate’s durability, corrosion resistance, and aesthetic qualities by adding a thin layer of a different metal.
Why choose coating over plating?
Choosing coating over plating can be advantageous for cost efficiency, environmental friendliness, and versatility in materials and finishes. Coatings can be applied to a broader range of substrates and are often easier to customize for specific applications.
What are the environmental impacts of plating?
Plating processes, especially those involving heavy metals like chromium or cadmium, can pose significant environmental risks. These include toxic waste production and hazardous emissions, necessitating strict compliance with environmental regulations.
Can plating enhance electrical conductivity?
Yes, plating can significantly enhance the electrical conductivity of a surface. Metals like gold and silver are commonly used in electronic components to ensure efficient electrical connections due to their excellent conductive properties.
Conclusion
The decision between coating and plating involves a nuanced understanding of material science and engineering applications. Each method offers distinct advantages that cater to specific industrial needs, whether it’s enhancing aesthetic appeal, improving wear resistance, or ensuring environmental sustainability.
As technology progresses, the development of more advanced and environmentally friendly surface treatment methods will likely continue to evolve. This progression will enhance the performance and sustainability of products across a multitude of industries, ultimately benefiting both manufacturers and consumers.