The terms calcination and sintering frequently appear in discussions surrounding materials science, metallurgy, and industrial manufacturing, each playing a pivotal role in the transformation of raw materials into finished products. While both processes involve the application of heat, they serve distinct purposes and operate under different conditions. The differentiation between the two is not just academic but practical, with significant implications for product quality, energy efficiency, and environmental impact.
Calcination and sintering are thermal treatments used to modify the physical and chemical properties of materials. Calcination typically involves heating a substance in the presence or absence of air to induce thermal decomposition or phase transition, excluding melting and sintering. On the other hand, sintering involves heating particles below their melting point to facilitate bonding, enhancing strength, and structural integrity without altering the material’s bulk composition.
The importance of these processes extends across various industries, including ceramics, metallurgy, and environmental technology. Calcination is critical for producing cement, lime, and ceramics, facilitating decomposition and the removal of volatile substances. Sintering, conversely, is essential for manufacturing complex-shaped components in powder metallurgy and ceramics, enabling particles to bond and densify. Understanding the nuances of each method provides insights into their applications, benefits, and limitations, shaping advancements in materials engineering and manufacturing processes.
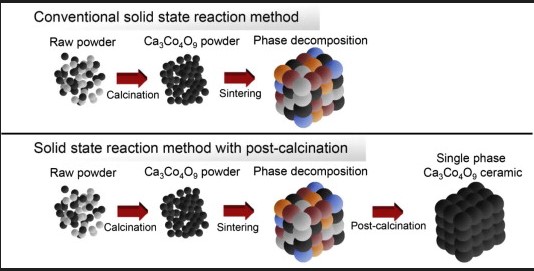
Calcination Explained
Definition and Basics
Calcination is a thermal treatment process widely used in the field of materials science and metallurgy. This process involves heating a solid material to a temperature that is below its melting point but high enough to induce thermal decomposition or a phase transition. The goal of calcination is often to drive off volatile substances, decompose raw materials, or remove moisture. It’s a critical step in the production of many materials, from metals to ceramics and cement.
Key Applications
Calcination plays a pivotal role in various industrial processes. For example:
- Cement Production: Limestone (calcium carbonate) is calcined to produce lime (calcium oxide), a key ingredient in cement.
- Refining Metals: Certain ores are calcined to remove impurities or volatile components before further processing.
- Manufacturing of Ceramics: Clay and other ceramic materials are often calcined to remove moisture and organic materials before shaping and firing.
- Production of Plaster: Gypsum, or calcium sulfate dihydrate, is calcined to produce plaster of Paris (calcium sulfate hemihydrate).
Process Parameters
Several factors influence the effectiveness and efficiency of the calcination process:
- Temperature: The specific temperature and duration of calcination depend on the material being processed.
- Atmosphere: Some materials require an oxygen-rich environment, while others need a controlled or reduced oxygen atmosphere.
- Material Size: The size and uniformity of the material particles can affect the heat transfer and reaction rates.
Sintering Unpacked
Definition and Overview
Sintering is another crucial thermal process used to create solid structures from powders. It involves heating materials to a temperature below their melting point, causing the particles to bond together. Sintering enhances the strength, structural integrity, and electrical conductivity of materials without significantly altering their composition.
Industrial Uses
Sintering has broad applications across many sectors:
- Powder Metallurgy: Used to create complex, high-strength components from metal powders.
- Ceramics: Produces dense, durable ceramic goods for use in electronics, aerospace, and medical implants.
- Electronics: Sintering is used to manufacture components such as multilayer ceramic capacitors (MLCCs) and other electronic devices.
Process Conditions
The sintering process is influenced by several key parameters:
- Temperature: Must be carefully controlled to promote particle bonding without reaching the melting point of the material.
- Time: The duration of sintering affects the density and properties of the final product.
- Atmosphere: An inert, reducing, or vacuum atmosphere may be required to prevent oxidation or other unwanted reactions.
Core Differences
Temperature Range
Calcination and sintering operate within different temperature ranges. Calcination typically occurs at temperatures from 500°C to about 1200°C, whereas sintering temperatures are higher, often between 1200°C and 1700°C, depending on the materials involved.
Atmosphere and Environment
The atmosphere is another point of divergence. Calcination might require air or an oxidizing atmosphere for effective decomposition, while sintering often takes place in a controlled, reducing, or inert atmosphere to facilitate particle bonding without oxidation.
Material Transformation
Calcination results in chemical changes, such as decomposition or phase transitions. In contrast, sintering mainly affects the physical properties, increasing density and strength through particle bonding.
Energy Consumption
The energy required for calcination and sintering varies. Calcination can be less energy-intensive if the target reaction occurs at lower temperatures. Sintering, requiring higher temperatures and sometimes prolonged heating, often consumes more energy.
Comparative Analysis
Impact on Material Properties
Both processes significantly alter material properties, but in different ways. Calcination is key for changing chemical composition and phase, while sintering is crucial for enhancing mechanical properties, such as strength and density.
Efficiency and Sustainability
Recent advancements aim to improve the energy efficiency of both processes. Innovations in process design, heat recovery, and the use of alternative fuels contribute to more sustainable practices in calcination and sintering.
Cost Implications
The cost of calcination and sintering is influenced by energy consumption, material handling, and process complexity. While both are essential, optimizing these processes can lead to significant cost savings and environmental benefits.
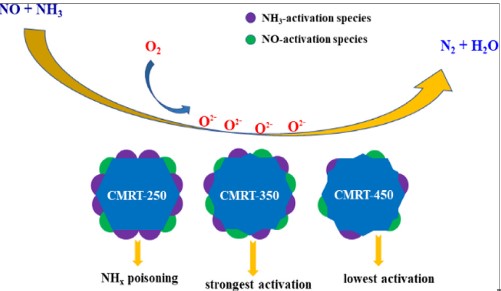
Sector-Specific Applications
Ceramics and Glass
The ceramics and glass industry heavily relies on both calcination and sintering for product development and refinement. Calcination is used to purify raw materials, like kaolin into calcined kaolin, which then becomes a critical ingredient in producing ceramic products with improved properties. Similarly, sintering plays an indispensable role in the production of ceramic and glass components, enhancing their structural integrity and durability. This process is particularly vital in creating highly specialized products such as bio-ceramics used in medical implants, and gorilla glass, known for its high strength and scratch resistance, pivotal in consumer electronics.
Metals and Alloys
In the metals and alloys sector, calcination serves as a preparatory step for extracting and refining metals from their ores. For instance, the calcination of bauxite is a key step in the Bayer process for aluminum production. Sintering, on the other hand, is crucial in powder metallurgy, which involves forming metal powders into dense solid parts. This technique allows for the manufacturing of complex shapes that would be challenging or impossible to achieve through traditional metalworking methods. High-performance parts for automotive, aerospace, and tooling applications often benefit from the unique properties imparted by the sintering process.
Environmental Technology
Environmental technology benefits from both calcination and sintering, particularly in waste management and air and water purification systems. Calcination is employed to stabilize hazardous waste, making it safer for disposal. It also plays a role in the regeneration of spent catalysts used in industrial processes. Sintering contributes to the development of filters and membranes for air and water purification systems, improving efficiency and durability while reducing maintenance costs and environmental impact.
Technological Advances
Innovations in Calcination
Recent innovations in calcination technology have focused on improving energy efficiency and reducing carbon emissions. One significant development is the introduction of solar thermal calcination processes, which utilize concentrated solar power to generate the high temperatures required for calcination, dramatically reducing the need for fossil fuels. Additionally, advancements in kiln design, such as regenerative kilns, offer enhanced heat recovery capabilities, further optimizing energy use and lowering operational costs.
Breakthroughs in Sintering Techniques
Breakthroughs in sintering techniques have been equally transformative, particularly the advent of spark plasma sintering (SPS). This method applies a pulsed electrical current directly to the powder material, significantly reducing the sintering time and energy consumption compared to conventional methods. Such innovations not only enhance the mechanical properties of the sintered materials but also open up new possibilities for the fabrication of novel materials, including nanocomposites and advanced ceramics with superior performance characteristics.
Future Directions
Research Trends
Current research trends in calcination and sintering are heavily focused on sustainability and efficiency. Scientists are exploring the use of alternative, less carbon-intensive fuels for calcination and investigating the potential of microwave and laser sintering as faster, more energy-efficient methods. There’s also a growing interest in developing processes that can accommodate a broader range of materials, including those derived from recycled or waste sources, to reduce the environmental footprint of these industrial processes.
Sustainable Practices
The drive towards sustainable practices is reshaping the calcination and sintering landscapes. This includes not only the adoption of green energy sources and the optimization of process parameters for energy conservation but also the integration of these processes into circular economy models. By enhancing material recyclability and extending the life cycle of products through improved design and manufacturing techniques, the industries reliant on calcination and sintering are moving closer to achieving their sustainability goals. Efforts to reduce waste and emissions, coupled with advancements in process efficiency, promise to further solidify the role of these thermal treatments in the future of sustainable manufacturing.
Frequently Asked Questions
What materials can be calcined?
Calcination can process a wide range of materials, including limestone (to produce lime), bauxite (for producing alumina), gypsum (to make plaster), and various ores and minerals for refining purposes. The process is versatile, adaptable to both organic and inorganic substances that undergo thermal decomposition.
How does sintering affect material properties?
Sintering significantly enhances the mechanical properties of materials, including strength, ductility, and thermal conductivity. By heating particles just below their melting points, sintering facilitates particle bonding without liquefying the material, leading to denser and more robust products.
Can calcination and sintering be environmentally friendly?
Both processes can be designed to minimize environmental impact through the use of renewable energy sources, recycling of heat, and reduction of emissions. Innovations in process control and material handling are continually reducing the carbon footprint of these essential industrial processes.
What are the main differences between calcination and sintering?
The main differences lie in their operating temperatures, atmosphere, material changes, and energy consumption. Calcination usually occurs at lower temperatures and often in an oxidizing atmosphere, focusing on decomposition or phase changes. Sintering happens at higher temperatures under controlled atmospheres, promoting particle fusion without melting.
Conclusion
The distinction between calcination and sintering underscores the complexity and versatility of thermal processes in material science. By altering physical and chemical properties, these methods are indispensable for achieving desired material characteristics, fulfilling the demands of various industrial applications. As technology progresses, so too will the efficiency and environmental sustainability of these processes, highlighting the importance of ongoing research and development.
Future advancements are likely to focus on optimizing energy consumption, reducing emissions, and enhancing material properties. Such improvements will not only benefit the industries reliant on these processes but will also contribute to a more sustainable and efficient manufacturing landscape, demonstrating the enduring significance of calcination and sintering in modern industrial practices.