.
Welding, an essential process in the construction and manufacturing industry, hinges on the effective management of two critical parameters: voltage and amperage. These elements play pivotal roles in determining the quality, strength, and durability of welds. By understanding their interplay, welders can manipulate the welding arc to suit various materials and thicknesses, ensuring optimal outcomes.
The relationship between voltage and amperage in welding is fundamental yet intricate. Voltage, or the electrical potential difference, influences the arc’s stability and heat input, while amperage, the current flow rate, affects penetration depth and weld bead size. Together, they determine the welding current, which must be finely tuned to achieve the desired weld characteristics, including strength, appearance, and integrity.
Focusing on the intricacies of voltage and amperage unveils the science behind successful welding practices. This knowledge not only empowers welders to make informed adjustments to their equipment but also highlights the importance of precision in creating strong, reliable welds. As we delve into the specifics, it becomes clear that mastering these parameters is crucial for anyone looking to excel in the welding field.
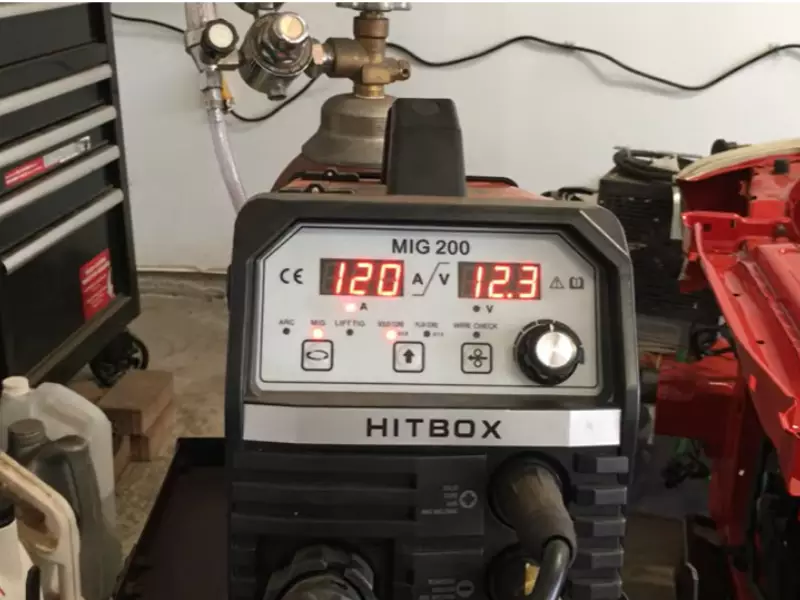
Basics of Welding Current
Voltage in Welding
Definition and Role
Voltage, often termed as electrical pressure, plays a pivotal role in welding operations. It determines the arc length and, consequently, the heat’s intensity applied to the metal. A welding arc is essentially an electrical circuit where the voltage drives the current through the air gap between the electrode and the workpiece, creating the heat necessary for welding.
Impact on Welding Arc
The voltage setting affects the stability and shape of the welding arc. Higher voltages produce a longer arc with more spread, suitable for deeper penetration in thicker materials. Conversely, lower voltages result in a shorter arc, offering more control and precision for thin materials. The correct voltage setting is crucial for achieving the desired weld bead characteristics and penetration.
Amperage in Welding
Definition and Significance
Amperage, or current, measures the flow of electricity through the welding circuit. It directly influences the welding speed and the amount of heat generated. Higher amperage settings increase the heat, allowing for deeper penetration into the workpiece. It’s fundamental in determining the strength and quality of the weld.
Effects on Penetration and Weld Strength
The amperage level is key to controlling weld penetration and joint strength. Optimal amperage settings ensure sufficient heat to properly melt the base metals, creating a strong, cohesive bond. Too low amperage may lead to poor penetration and weak welds, while too high amperage can cause excessive penetration, undercut, and other weld defects.
Interplay of Voltage and Amperage
Direct Relationship
Voltage and amperage have a direct relationship in welding. Adjusting one often requires adjustments to the other to maintain the desired weld quality. For instance, increasing voltage typically necessitates an increase in amperage to sustain arc stability and penetration depth.
Practical Implications for Welders
Welders must understand this relationship to effectively control the welding process. This knowledge allows for the adjustment of settings to achieve the optimal heat input, arc characteristics, and weld bead appearance for various materials and thicknesses.
Balancing Act
Adjusting Voltage and Amperage for Different Materials
Different materials and thicknesses require specific voltage and amperage settings. For example, aluminum requires a higher amperage than steel for effective welding due to its higher thermal conductivity. Welders must adjust both settings to accommodate the material’s properties, ensuring quality welds without damaging the workpiece.
Importance of Finding the Right Balance
Finding the right balance between voltage and amperage is essential for optimal weld performance. This balance ensures efficient heat input, reducing the risk of defects such as porosity, cracking, or distortion. A well-balanced weld has good penetration, a smooth bead profile, and is free of defects, ensuring structural integrity and aesthetic appeal.
Factors Influencing Voltage and Amperage
Material Thickness
Influence on Required Amperage
The thickness of the material being welded significantly influences the required amperage. Thicker materials need higher amperage for adequate penetration, while thinner materials require lower amperage to prevent burn-through. Adjusting the amperage according to material thickness is crucial for producing strong, defect-free welds.
Adjustments in Voltage for Effective Welding
Similarly, voltage adjustments are necessary when welding materials of different thicknesses. Higher voltage settings can help manage the wider arc needed for thick materials, while lower settings are better suited for thin materials, providing greater control and reducing the risk of heat damage.
Welding Positions
Challenges in Different Positions
Welding positions (flat, horizontal, vertical, or overhead) present unique challenges that affect voltage and amperage settings. Overhead and vertical positions, for instance, might require lower amperage to prevent sagging or dripping of the weld pool.
Adjusting Voltage and Amperage Accordingly
Adapting voltage and amperage for different positions ensures consistent weld quality across various orientations. This adaptation is crucial for maintaining arc stability and penetration, regardless of the welding position.
Type of Welding
Variations in Requirements for MIG, TIG, and Stick Welding
Each welding process (MIG, TIG, Stick) has distinct voltage and amperage requirements based on the electrode type, shielding gas, and desired weld characteristics. MIG welding, for example, typically operates at higher amperage and voltage compared to TIG welding, which focuses on precision and control.
Tailoring Voltage and Amperage Settings
Tailoring these settings to the specific welding process and application is essential for achieving the desired weld quality. Understanding the unique demands of each process allows welders to adjust voltage and amperage for optimal results, whether seeking deep penetration with MIG or fine detail with TIG welding.
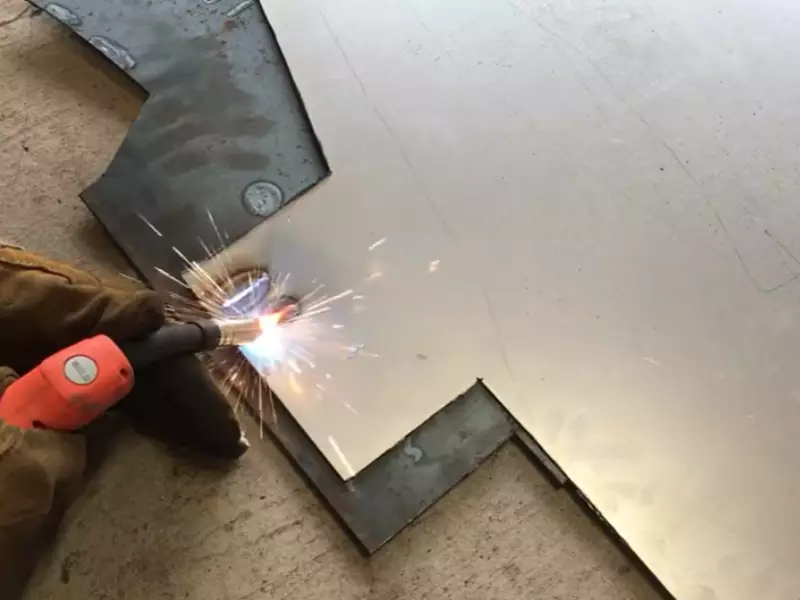
Setting Up for Success
Equipment Considerations
Choosing the Right Welder
Selecting the appropriate welder is the first step toward successful welding projects. The choice depends on various factors, including the type of welding (MIG, TIG, Stick), material thickness, and work environment. A versatile welder that accommodates different materials and thicknesses is ideal for both beginners and experienced welders.
Importance of Adjustable Settings
Welders with adjustable voltage and amperage settings offer greater control over the welding process, allowing for fine-tuning based on the specific requirements of each project. This flexibility is crucial for achieving optimal weld quality and efficiency, especially when working with a variety of materials and thicknesses.
Safety Measures
Role of Voltage and Amperage in Safe Welding Practices
The settings of voltage and amperage not only affect the quality of the weld but also the safety of the welding process. Incorrect settings can lead to unstable arcs, spatter, and excessive heat, posing risks to the welder. Understanding and applying the right settings can minimize these risks, contributing to a safer welding environment.
Personal Protective Equipment and Precautions
- Welding helmets with auto-darkening lenses protect eyes from harmful arc rays and improve visibility.
- Gloves and protective clothing shield against sparks, spatter, and UV radiation.
- Ensuring adequate ventilation reduces exposure to harmful fumes and gases.
- Ear protection guards against noise from grinding and welding operations.
Optimizing Weld Quality
Experimentation and Practice
The key to mastering welding is consistent practice and experimentation with different settings. Trying out various combinations of voltage and amperage on scrap material allows welders to understand how adjustments affect the weld. This hands-on experience is invaluable for developing the skills to produce high-quality welds consistently.
Learning from Experience and Mistakes
Mistakes are inevitable in the learning process, but they offer critical learning opportunities. Whether it’s dealing with cracks, porosity, or improper penetration, each error provides insights into what adjustments are needed. Reflecting on these mistakes and understanding their causes enhances a welder’s ability to prevent them in future projects.
Professional Tips
Advice from Seasoned Welders
Experienced welders often emphasize the importance of cleanliness (both of the workpiece and the equipment), the right angle of approach, and the speed of travel. These factors, combined with proper voltage and amperage settings, are crucial for achieving strong, clean welds. Listening to the arc and watching the weld pool can also provide real-time feedback for adjustments.
Common Pitfalls to Avoid
- Ignoring material prep: Failing to clean the material properly can lead to contamination and weak welds.
- Overlooking equipment maintenance: Regularly check and maintain welding equipment for consistent performance.
- Inadequate practice: Underestimating the value of practice on scrap materials before starting on the actual workpiece can result in poor-quality welds.
- Rigid adherence to settings: Not adjusting the settings for different materials or positions often leads to suboptimal welds. Flexibility and adaptability are key.
Frequently Asked Questions
How does voltage affect welding?
Voltage in welding primarily impacts the arc’s stability and the heat input into the material. Higher voltages result in a longer arc, which can increase the width of the weld and decrease penetration. Conversely, lower voltages produce a shorter arc, focusing the heat more intensely and increasing penetration. Adjusting the voltage allows welders to control the arc characteristics and adapt to different welding tasks.
What role does amperage play in welding?
Amperage, or the flow of electric current, in welding directly influences the weld bead’s depth of penetration and the overall heat generated. A higher amperage setting increases penetration and heat input, making it suitable for thicker materials. Lower amperage settings reduce heat and penetration, ideal for welding thinner materials or when precision is paramount. Understanding how to adjust amperage is vital for achieving the desired weld quality.
Can voltage and amperage be adjusted independently?
Yes, voltage and amperage can be adjusted independently in most welding machines. This allows welders to fine-tune the welding parameters to match the specific requirements of the job at hand, such as material thickness, welding position, and desired weld characteristics. Independent adjustment is crucial for versatility and achieving optimal results across a wide range of welding applications.
Why is finding the right balance between voltage and amperage important?
Finding the right balance between voltage and amperage is crucial for producing high-quality welds. The correct settings ensure the right combination of arc stability, penetration depth, and heat input, which are essential for the integrity and strength of the weld. An imbalance can lead to defects such as excessive spatter, poor penetration, or excessive heat input, compromising the weld’s quality.
Conclusion
The art and science of welding demand a deep understanding of the relationship between voltage and amperage. As we’ve explored, these two parameters are the linchpins of successful welding, affecting everything from arc stability to penetration depth and overall weld quality. Welders who master the delicate balance between voltage and amperage can adapt to various materials and conditions, ensuring their work not only holds up under scrutiny but stands the test of time.
In conclusion, the journey to becoming a proficient welder is marked by a continuous learning process, where knowledge of voltage and amperage plays a critical role. By embracing the complexities of these parameters, welders can enhance their skills, improve their techniques, and contribute to the advancement of the welding industry. The relationship between voltage and amperage is not just a technical detail; it is the foundation upon which skilled welders build their craft.